Sleeve type continuous calcining vertical kiln
A sleeve type and calcining technology, applied in the field of high temperature calcination production, can solve the problems such as the inability to continuously produce lime kilns, reduce the production efficiency of lime kilns, and affect product quality, etc., and achieve the effects of good energy saving, simple structure and convenient control.
- Summary
- Abstract
- Description
- Claims
- Application Information
AI Technical Summary
Problems solved by technology
Method used
Image
Examples
Embodiment Construction
[0015] The specific embodiment of sleeve type continuous calcination shaft kiln of the present invention is as figure 1 As shown, the direction of the arrow in the figure is the airflow direction. The kiln body of the shaft kiln is mainly composed of a cylindrical furnace shell 1 made of thermal insulation material installed on the base 14 and an outer cylinder 2 and an inner cylinder 3 coaxially sleeved in the furnace shell 1 and made of refractory materials. , the inner cylinder 3, the outer cylinder 2 and the furnace shell 1 together form a three-layer sleeve kiln structure, wherein the inner cylinder 3 and the outer cylinder 2 are mainly composed of refractory bricks layer by layer, and the inner cavity of the inner cylinder 3 An axially extending hollow pipe 6 is formed, an axially extending annular furnace chamber 5 is formed between the inner cylinder 3 and the outer cylinder 2, and an axially extending annular periphery is formed between the furnace shell 1 and the out...
PUM
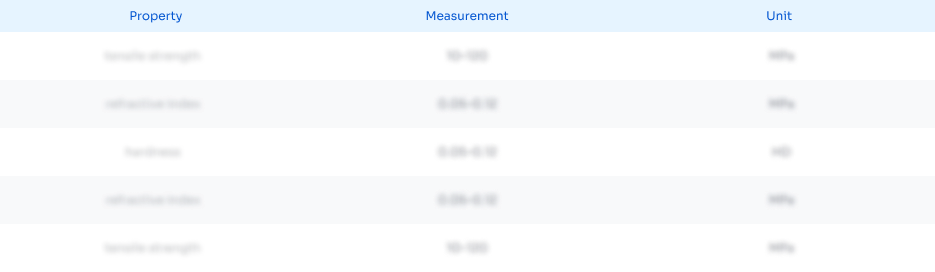
Abstract
Description
Claims
Application Information

- R&D
- Intellectual Property
- Life Sciences
- Materials
- Tech Scout
- Unparalleled Data Quality
- Higher Quality Content
- 60% Fewer Hallucinations
Browse by: Latest US Patents, China's latest patents, Technical Efficacy Thesaurus, Application Domain, Technology Topic, Popular Technical Reports.
© 2025 PatSnap. All rights reserved.Legal|Privacy policy|Modern Slavery Act Transparency Statement|Sitemap|About US| Contact US: help@patsnap.com