Manufacturing method and manufacturing system for solar cell back plate
A technology of solar cells and manufacturing methods, applied in chemical instruments and methods, circuits, photovoltaic power generation, etc., can solve problems such as complex production process of solar cell backplanes, hidden dangers of production safety, threats to personal health, etc., and achieve good operability, Excellent solvent resistance and excellent chemical resistance
- Summary
- Abstract
- Description
- Claims
- Application Information
AI Technical Summary
Problems solved by technology
Method used
Image
Examples
Embodiment 1
[0059] Combine figure 2 As shown, the first unwinding device 11 and the second unwinding device 12 are respectively installed with the first film material 111 and the second film material 121 in the roll, and the first film material 111 passes through the first tension device 21 to keep the film material flat. The wrinkles are then passed through a pretreatment device 80 to remove static electricity and dust on the surface of the first membrane 111. After the first film 111 passes through the first tension device 11 and the pretreatment device 80, it then passes between the heating type coating device 30 and the pressure roller A, and the heating type coating device 30 faces the surface of the first film 111. Coating reactive hot melt adhesive heated into a fluid state. The heating type coating device 30 is connected to a hot melt glue machine (not shown in the figure) through a glue pipe. The hot melt glue machine is continuously heated to produce a fluid state of reactive ho...
Embodiment 2
[0065] The only difference between Example 2 and Example 1 is that the heating-type coating device 30 in Example 1 is specifically selected as a heating non-marking scraper 30A with a rotating flat round bar, while in Example 2 the heating-type coating device The device 30 is implemented as a combination of a scraper 31 and a heated mesh roller 32, namely figure 2 Replace the part in the dashed box with Figure 4 The structure shown.
[0066] Combine Figure 4 ~ Figure 5 As shown, the heating-type coating device 30 is composed of a doctor blade 31 and a heating-type dot-shaped drum 32 arranged oppositely, and the heating-type dot-shaped drum 32 is tangent to the pressing wheel A. Before starting the manufacturing system of this embodiment, the hot melt glue machine is turned on, and the gap between the scraper 31 and the heated mesh roller 32 is adjusted to control the amount of glue. First, turn on the heating system matching the heating type mesh roller 32 and the scraper 31,...
PUM
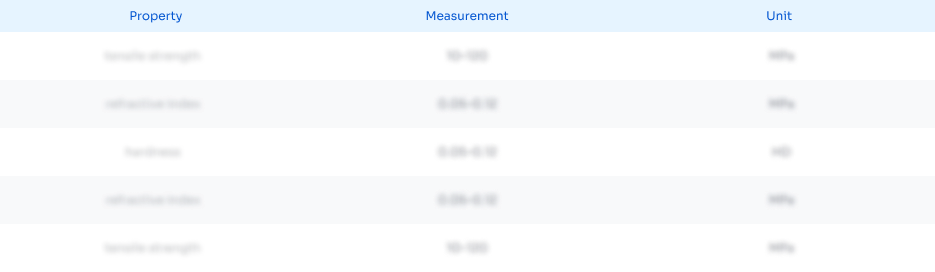
Abstract
Description
Claims
Application Information

- Generate Ideas
- Intellectual Property
- Life Sciences
- Materials
- Tech Scout
- Unparalleled Data Quality
- Higher Quality Content
- 60% Fewer Hallucinations
Browse by: Latest US Patents, China's latest patents, Technical Efficacy Thesaurus, Application Domain, Technology Topic, Popular Technical Reports.
© 2025 PatSnap. All rights reserved.Legal|Privacy policy|Modern Slavery Act Transparency Statement|Sitemap|About US| Contact US: help@patsnap.com