Lithium-sulfur battery self-supporting cathode material and electro-spinning preparation method thereof
A cathode material, lithium-sulfur battery technology, applied in battery electrodes, lithium batteries, positive electrodes, etc., can solve the uncontrollable influence of electrode material flexibility factors, affect the electrochemical performance of lithium-sulfur batteries, and the poor conductivity of active material sulfur, etc. It can improve the electrochemical performance, alleviate the shuttle effect, and improve the chemical adsorption force.
- Summary
- Abstract
- Description
- Claims
- Application Information
AI Technical Summary
Problems solved by technology
Method used
Image
Examples
preparation example Construction
[0028] A kind of electrospinning preparation method of lithium-sulfur battery self-supporting cathode material of the present invention, comprises the following steps:
[0029] (1) Dissolve polymethyl methacrylate (PMMA) directly in N,N-dimethylformamide, heat and stir evenly, then add polyacrylonitrile (PAN), heat and stir evenly, and obtain the precursor of electrospinning liquid.
[0030] (2) An electrospun fiber film containing polyacrylonitrile and polymethyl methacrylate was prepared by electrospinning and collected by a rotating shaft receiver.
[0031] (3) Pre-oxidizing and carbonizing the material obtained in step (2) to obtain an in-situ nitrogen-doped porous carbon fiber film.
[0032] (4) The in-situ nitrogen-doped porous carbon fiber film obtained in step (3) is immersed in a certain concentration of sulfur in a carbon disulfide solution, and after drying, heat treatment is carried out under an argon atmosphere to obtain a self-supporting lithium-sulfur battery p...
Embodiment 1
[0040] Step 1: Dissolve 0.2g polymethyl methacrylate (PMMA) in 10mL N,N-dimethylformamide, stir until dissolved evenly, then add 0.6g polyacrylonitrile (PAN), stir magnetically at 60°C , and stirred until the solution was bright yellow to obtain a spinning precursor.
[0041] Step 2: Set the parameters of electrospinning: the voltage is 14kV, the rotational speed of the rotating shaft receiver is 300r / min, the receiving distance is 15cm, and the advancing speed of the syringe is 2mm / h. After 8 hours of electrospinning, the electrospun fiber film can be obtained.
[0042] Step 3: Pre-oxidize the obtained electrospun fiber film at 220° C. for 1 hour in an air atmosphere in a tube furnace with a heating rate of 1° C. / min.
[0043] Step 4: Carbonize the pre-oxidized film at 600° C. for 2 hours under an argon atmosphere, with a heating rate of 5° C. / min. The in-situ nitrogen-doped porous carbon fiber film can be obtained.
[0044] Step 5: Prepare a sulfur-carbon disulfide soluti...
Embodiment 2
[0046] Step 1: Dissolve 0.2g polymethyl methacrylate (PMMA) in 10mL N,N-dimethylformamide, stir until dissolved evenly, then add 0.7g polyacrylonitrile (PAN), stir magnetically at 70°C , and stirred until the solution was bright yellow to obtain a spinning precursor.
[0047] Step 2: Set the parameters of electrospinning: the voltage is 15kV, the rotational speed of the rotating shaft receiver is 400r / min, the receiving distance is 16cm, and the advancing speed of the syringe is 3mm / h. After 8 hours of electrospinning, the electrospun fiber film can be obtained.
[0048]Step 3: Pre-oxidize the obtained electrospun fiber film at 280° C. for 1.5 h in an air atmosphere in a tube furnace with a heating rate of 1° C. / min.
[0049] Step 4: Carbonize the pre-oxidized film at 800° C. for 1.5 h under an argon atmosphere, with a heating rate of 5° C. / min. The in-situ nitrogen-doped porous carbon fiber film can be obtained.
[0050] Step 5: Prepare a sulfur-carbon disulfide solution w...
PUM
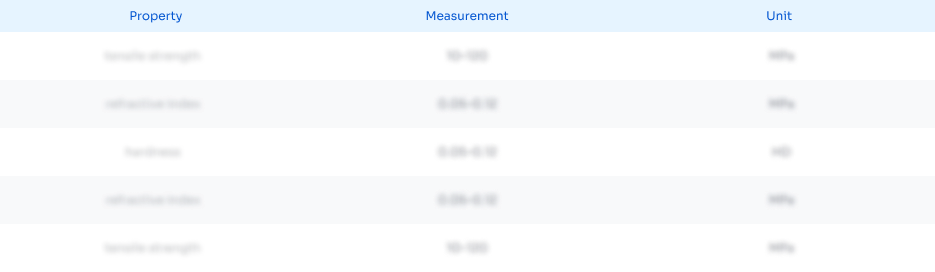
Abstract
Description
Claims
Application Information

- R&D
- Intellectual Property
- Life Sciences
- Materials
- Tech Scout
- Unparalleled Data Quality
- Higher Quality Content
- 60% Fewer Hallucinations
Browse by: Latest US Patents, China's latest patents, Technical Efficacy Thesaurus, Application Domain, Technology Topic, Popular Technical Reports.
© 2025 PatSnap. All rights reserved.Legal|Privacy policy|Modern Slavery Act Transparency Statement|Sitemap|About US| Contact US: help@patsnap.com