Polyphenylene sulfide navy-blue masterbatches, polyphenylene sulfide navy-blue colored fiber and preparation methods of polyphenylene sulfide navy-blue masterbatches and polyphenylene sulfide navy-blue colored fiber
A technology of polyphenylene sulfide and colored fibers, which is applied in the fields of polyphenylene sulfide fibers, polyphenylene sulfide navy blue masterbatch, colored fibers and preparation fields, can solve the problems of low color fastness, etc., and improve the processing technology. condition, good compatibility, the effect of improving color performance
- Summary
- Abstract
- Description
- Claims
- Application Information
AI Technical Summary
Problems solved by technology
Method used
Image
Examples
Embodiment 1
[0044] This embodiment provides a polyphenylene sulfide navy blue color masterbatch, which consists of the following raw materials in parts by weight: 10% of colorant nano-powder, 3% of hyperdispersant, and 0.1% of antioxidant , PPS powder is 86.9%.
[0045] The coloring agent nano powder is composed of the following raw materials in parts by weight: 20% of ultramarine blue, 45% of phthalocyanine blue 15:3, and 35% of carbon black.
[0046] The preparation method of polyphenylene sulfide masterbatch in the present embodiment, this method comprises the following steps:
[0047]Step 1.1: Grind the colorant nano-powder with a planetary ball mill for 1 hour, then prepare a DMF solvent dispersion with a mass concentration of 20% colorant, heat it at 70°C and a stirring speed of 60 rpm for 30-40 minutes for pre-dispersion, and then Add hyperdispersant and continue to stir for 150min to 180min, filter and dry to obtain a modified colorant for later use;
[0048] Step 1.2: Add antio...
Embodiment 2
[0058] This embodiment provides a polyphenylene sulfide navy blue color masterbatch, which is composed of the following raw materials in parts by weight: 15% of colorant nano powder, 4% of hyperdispersant, and 0.3% of antioxidant , PPS powder is 80.7%.
[0059] The formula of coloring agent nanopowder is identical with embodiment 1.
[0060] The preparation method of the polyphenylene sulfide color masterbatch in this embodiment is basically the same as that in Embodiment 1.
[0061] This example also provides a preparation method of polyphenylene sulfide navy blue colored fiber, the raw material formula of the polyphenylene sulfide colored fiber used in this method is the same as that in Example 1. The specific steps included in this method are basically the same as those in Example 1.
Embodiment 3
[0063] This embodiment provides a polyphenylene sulfide navy blue color masterbatch, which consists of the following raw materials in parts by weight: 20% of colorant nano-powder, 5% of hyperdispersant, and 0.5% of antioxidant , PPS powder is 74.5%.
[0064] The formula of coloring agent nanopowder is identical with embodiment 1.
[0065] The preparation method of the polyphenylene sulfide color masterbatch in this embodiment is basically the same as that in Embodiment 1.
[0066] This example also provides a preparation method of polyphenylene sulfide navy blue colored fiber, the raw material formula of the polyphenylene sulfide colored fiber used in this method is the same as that in Example 1. The specific steps included in this method are basically the same as those in Example 1.
PUM
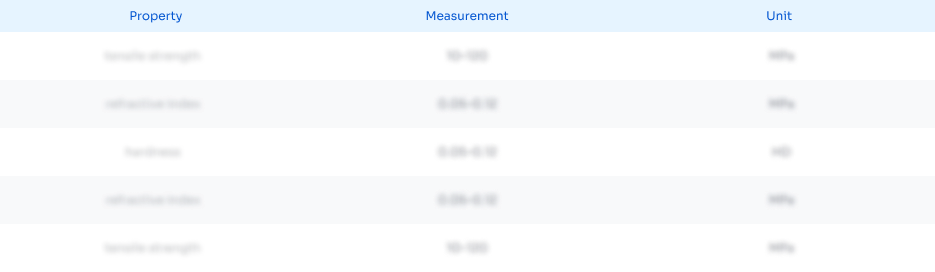
Abstract
Description
Claims
Application Information

- R&D Engineer
- R&D Manager
- IP Professional
- Industry Leading Data Capabilities
- Powerful AI technology
- Patent DNA Extraction
Browse by: Latest US Patents, China's latest patents, Technical Efficacy Thesaurus, Application Domain, Technology Topic, Popular Technical Reports.
© 2024 PatSnap. All rights reserved.Legal|Privacy policy|Modern Slavery Act Transparency Statement|Sitemap|About US| Contact US: help@patsnap.com