Production technology for necking textile
A production process and textile technology, applied in the field of textile shrinkage production process, can solve the problems of elastic band limit fatigue, limited webbing elasticity, loss of resilience, etc., to ensure stickiness and durability, improve fastness, and ensure firmness Effect
- Summary
- Abstract
- Description
- Claims
- Application Information
AI Technical Summary
Problems solved by technology
Method used
Image
Examples
Embodiment 1
[0041] A seamless sculpture elastic band production equipment, such as figure 1 and figure 2 As shown, the equipment includes a rotary turntable 1, and a material preparation area 2, a pre-setting area 3 and a shaping area 4 are sequentially arranged on the circumference of the rotary turntable 1. A lower mold 5 is all arranged in the areas of the material preparation area 2, the pre-setting area 3 and the shaping area 4, the lower molds 5 are distributed in a circle and the angle between two adjacent lower molds 5 is 120 degrees. Lower mold 5 is for the placement of raw materials in the process of processing.
[0042] Such as figure 1 As shown, a mounting bracket 6 is also included, and the mounting bracket 6 includes a support rod 7 arranged vertically at the center of the rotary turntable 1 and a side arm 8 that is horizontally connected to the support rod 7, and the support rod 7 passes through Set in the hole in the center of the turntable, the support rod 7 and the r...
Embodiment 2
[0049] A kind of production technology of textile necking, such as Figure 5 As shown, the materials used in the process are as follows:
[0050] (1) Prepare the base fabric, webbing and hot-melt adhesive film.
[0051] Base fabric, the base fabric is made of chemical fiber, which should be elastic, and silicon soft treatment is strictly prohibited.
[0052] Hot-melt adhesive film, select the hot-melt adhesive film with low melting point and good viscosity for use, the types of hot-melt adhesive film that can be used in the present embodiment are as follows: Bemis 3415-6MIL, DZ 3258-6MIL, DZ 6585-6MIL, DZ 6625- 6MIL.
[0053] For the webbing, choose a webbing with high elasticity and a thinner body to improve the comfort and resilience after bonding, and silicon soft disposal is strictly prohibited.
[0054] According to the shape, the ribbon can be divided into a straight mouth and a double mouth. The straight mouth is a strip shape, and the double mouth is the side openin...
PUM
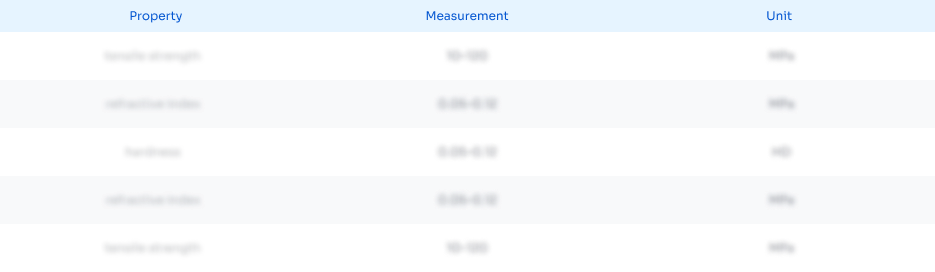
Abstract
Description
Claims
Application Information

- Generate Ideas
- Intellectual Property
- Life Sciences
- Materials
- Tech Scout
- Unparalleled Data Quality
- Higher Quality Content
- 60% Fewer Hallucinations
Browse by: Latest US Patents, China's latest patents, Technical Efficacy Thesaurus, Application Domain, Technology Topic, Popular Technical Reports.
© 2025 PatSnap. All rights reserved.Legal|Privacy policy|Modern Slavery Act Transparency Statement|Sitemap|About US| Contact US: help@patsnap.com