Equivalent thermal network modeling method of hybrid excitation axial magnetic field flux switching motor
A technology of magnetic flux switching motor and equivalent thermal network, which is applied in the fields of electrical digital data processing, instrumentation, calculation, etc., can solve the problem that the temperature field distribution of the hybrid excitation axial magnetic field flux switching motor is inconsistent in the axial direction and cannot correctly reflect the motor. temperature rise, lack of detailed analysis and calculation, etc., to reduce the difficulty, increase the speed of calculation, and achieve the effect of accurate calculation
- Summary
- Abstract
- Description
- Claims
- Application Information
AI Technical Summary
Problems solved by technology
Method used
Image
Examples
Embodiment
[0125] Combine figure 2 The motor used in the present invention is a 6 / 10-pole hybrid excitation axial flux switching motor. The motor adopts a double stator and single rotor structure, consisting of a stator 1, a rotor 2, a permanent magnet 3, an armature winding 4 and an excitation winding 5. Each stator 1 is composed of six E-type iron cores and six permanent magnets 3 alternately. The E-type iron core adopts parallel slots, and the permanent magnets 3 adopt parallel magnetization. The magnetization directions of adjacent permanent magnets 3 are opposite. The magnetization direction of the permanent magnet 3 on the side stator is also opposite; the armature winding 4 is wound on two adjacent stator teeth, and the field winding 5 is wound on the middle tooth of the E-shaped iron core; The group coils are connected in series to form a three-phase armature winding. The opposite in-phase armature coils on the stators on both sides are also connected in series; both the armature ...
PUM
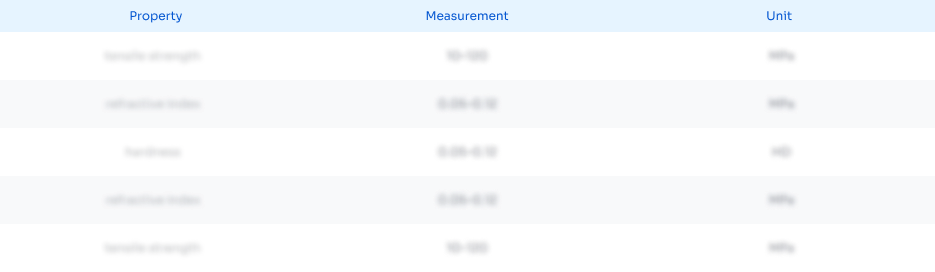
Abstract
Description
Claims
Application Information

- Generate Ideas
- Intellectual Property
- Life Sciences
- Materials
- Tech Scout
- Unparalleled Data Quality
- Higher Quality Content
- 60% Fewer Hallucinations
Browse by: Latest US Patents, China's latest patents, Technical Efficacy Thesaurus, Application Domain, Technology Topic, Popular Technical Reports.
© 2025 PatSnap. All rights reserved.Legal|Privacy policy|Modern Slavery Act Transparency Statement|Sitemap|About US| Contact US: help@patsnap.com