Method for etching surface microstructure of polytetrafluoroethylene material by using ion beam
A technology of polytetrafluoroethylene and ion beam etching, which is applied in the direction of microstructure technology, microstructure devices, manufacturing microstructure devices, etc., can solve the problems of PTFE processing microstructure, PTFE surface processing, photoresist can not adhere, etc.
- Summary
- Abstract
- Description
- Claims
- Application Information
AI Technical Summary
Problems solved by technology
Method used
Image
Examples
Embodiment 1
[0032] Such as figure 1 As shown, Embodiment 1 of the present invention provides a method for ion beam etching the surface microstructure of polytetrafluoroethylene materials, including the following process steps:
[0033] Process the hollow pattern 2 of the array on the mask plate 1; use the mask plate 1 with the hollow pattern 2 to cover the surface of the polytetrafluoroethylene material 3, so that the hollow pattern 2 is perpendicular to the surface of the polytetrafluoroethylene material 3 Mapping, as an effective etching area; use a parallel ion beam to carry out the first vertical bombardment on the surface of the polytetrafluoroethylene material 3 covered with the mask plate 1 for a certain time, and the ion beam passes through the effective etching area to make the polytetrafluoroethylene The surface of the vinyl material forms a first surface structure 4 consistent with the pattern of the effective etching area.
[0034] The mask plate 1 is made of stainless steel....
Embodiment 2
[0038] Embodiment 2 of the present invention provides a method for ion beam etching the surface microstructure of polytetrafluoroethylene materials, including the following process steps:
[0039] An array of hollow patterns 2 is processed on the mask plate 1; two layers of mask plates 1 with the same hollow pattern are used to cover the polytetrafluoroethylene material 3 in turn, and the two layers of mask plates 1 are vertical to the polytetrafluoroethylene material. The central axis of the tetrafluoroethylene material rotates at a certain angle for the rotation axis; the overlapping area of the hollow pattern between the two mask plates 1 is vertically mapped to the surface of the polytetrafluoroethylene material 3 as an effective etching area. Use the parallel ion beam to carry out the first vertical bombardment on the surface of the polytetrafluoroethylene material 3 covered with the mask plate 1 for a certain period of time, and the ion beam passes through the effective...
Embodiment 3
[0043] Such as Figure 5 As shown, implementation 3 of the present invention provides a method for ion beam etching the surface microstructure of polytetrafluoroethylene materials, including the following process steps:
[0044] Process the hollow pattern 2 of the array on the mask plate 1; use the mask plate 1 with the hollow pattern 2 to cover the surface of the polytetrafluoroethylene material 3, so that the hollow pattern 2 is perpendicular to the surface of the polytetrafluoroethylene material 3 Mapping, as an effective etching area; use a parallel ion beam to carry out the first vertical bombardment on the surface of the polytetrafluoroethylene material 3 covered with the mask plate 1 for a certain time, and the ion beam passes through the effective etching area to make the polytetrafluoroethylene The surface of the vinyl material forms a first surface structure 4 consistent with the pattern of the effective etching area; After the surface is rotated by a certain angle,...
PUM
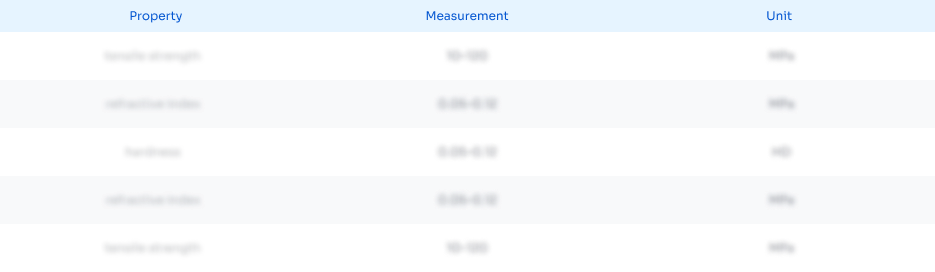
Abstract
Description
Claims
Application Information

- R&D
- Intellectual Property
- Life Sciences
- Materials
- Tech Scout
- Unparalleled Data Quality
- Higher Quality Content
- 60% Fewer Hallucinations
Browse by: Latest US Patents, China's latest patents, Technical Efficacy Thesaurus, Application Domain, Technology Topic, Popular Technical Reports.
© 2025 PatSnap. All rights reserved.Legal|Privacy policy|Modern Slavery Act Transparency Statement|Sitemap|About US| Contact US: help@patsnap.com