Method for preparing NiS@CC nano material by solvothermal
A nanomaterial and solvothermal technology, applied in the field of non-precious metal nanocomposite materials, can solve the problem of lack of high-performance non-precious metal electrocatalysts, and achieve the effect of low overpotential and large specific capacitance
- Summary
- Abstract
- Description
- Claims
- Application Information
AI Technical Summary
Problems solved by technology
Method used
Image
Examples
Embodiment 1
[0036] (1) Treatment of carbon cloth: The commercial carbon cloth was washed several times with acetone, distilled water and absolute ethanol in sequence, and dried at 60 °C for 6 h. Put the cleaned carbon cloth into a porcelain boat, then place it in a tube furnace, and heat it at 8 °C min in a nitrogen atmosphere. -1 Raise the temperature to 900°C for 1.5h, cool to room temperature; soak in concentrated hydrochloric acid for 2h, wash with distilled water and absolute ethanol several times until neutral, and vacuum dry at 60°C for 6h;
[0037](2) Preparation of NiS@CC nanomaterials: 1 mmol (290.79 mg) of nickel nitrate hexahydrate and 6 mmol (360 mg) of urea were dissolved in 15 mL of distilled water, and stirred at room temperature for 1 h. The mixed solution was transferred to a polytetrafluoroethylene reactor, and the treated carbon cloth (2 cm × 2 cm) was vertically placed in the mixed solution, and the reactor was sealed and placed in a dry box at 120 °C for hydrothermal...
Embodiment 2
[0040] (1) Treatment of carbon cloth: same as Example 1;
[0041] (2) Preparation of nanostructured NiS@CC-2 material: 1 mmol (290.79 mg) of nickel nitrate hexahydrate and 6 mmol (360 mg) of urea were dissolved in 15 mL of distilled water and stirred at room temperature for 1 h. The mixed solution was transferred to a polytetrafluoroethylene reactor, and the treated carbon cloth (2 cm × 2 cm) was vertically placed in the mixed solution, and the reactor was sealed and placed in a dry box at 120 °C for hydrothermal treatment. React for 12 hours; cool to room temperature, wash with distilled water and absolute ethanol several times, and vacuum-dry at 60°C for 6 hours to obtain the loaded precursor carbon cloth; dissolve 100 mg of sodium sulfide nonahydrate in 15 ml of distilled water, and stir at room temperature for 0.5 h; The mixed solution was transferred to a polytetrafluoroethylene reactor, and the carbon cloth loaded with the precursor carbon cloth was vertically placed in ...
Embodiment 3
[0044] (1) Treatment of carbon cloth: Sonicate commercial carbon cloth with acetone, distilled water and absolute ethanol for 2 hours respectively, and dry at 60°C for 6 hours;
[0045] (2) Preparation of nanostructured NiS@CC-3 material: 1 mmol (290.79 mg) of nickel nitrate hexahydrate and 6 mmol (360 mg) of urea were dissolved in 15 mL of distilled water and stirred at room temperature for 1 h. The mixed solution was transferred to a polytetrafluoroethylene reactor, and the treated carbon cloth (2 cm × 2 cm) was vertically placed in the mixed solution, and the reactor was sealed and placed in a dry box at 120 °C for hydrothermal treatment. React for 12 hours; cool to room temperature, wash with distilled water and absolute ethanol several times, and vacuum-dry at 60°C for 6 hours to obtain the loaded precursor carbon cloth; dissolve 90 mg of sodium sulfide nonahydrate in 15 mL of distilled water, and stir at room temperature for 0.5 h; The mixed solution was transferred to a...
PUM
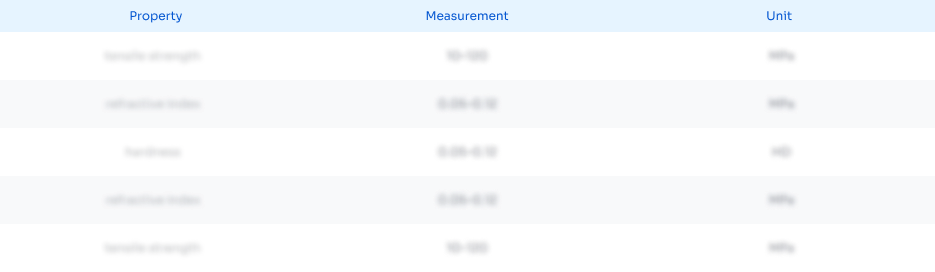
Abstract
Description
Claims
Application Information

- Generate Ideas
- Intellectual Property
- Life Sciences
- Materials
- Tech Scout
- Unparalleled Data Quality
- Higher Quality Content
- 60% Fewer Hallucinations
Browse by: Latest US Patents, China's latest patents, Technical Efficacy Thesaurus, Application Domain, Technology Topic, Popular Technical Reports.
© 2025 PatSnap. All rights reserved.Legal|Privacy policy|Modern Slavery Act Transparency Statement|Sitemap|About US| Contact US: help@patsnap.com