Unlikely-to-deform elastic blended woven tape
A webbing and elastic technology, applied in the field of fabric textiles, can solve the problems of poor elasticity, easy pilling, rough surface, etc., and achieve the effects of improving elasticity and resilience, good air permeability, and good dyeability
- Summary
- Abstract
- Description
- Claims
- Application Information
AI Technical Summary
Problems solved by technology
Method used
Image
Examples
Embodiment 1
[0033] Z1. Select 30 parts of raw material elastic yarn, 20 parts of cashmere fiber, 10 parts of mulberry silk, 8 parts of chitosan fiber, 6 parts of anti-mold and mothproof agent, and 12 parts of silver fiber. After selection, 30 parts of elastic yarn , 20 parts of cashmere fiber and 12 parts of silver fiber are respectively opened and carded by a fiber opening carding machine;
[0034] Z2. After combing, add it to the mixing mixer, continue to add 10 parts of mulberry silk, 8 parts of chitosan fiber and 6 parts of anti-mold and mothproofing agent to the mixing mixer. After stirring for 10 minutes, they are dehydrated and dried. After slicing, spinning, winding, and stretching, the synthetic fiber is formed, and the diameter of the synthetic fiber is 60um;
[0035] Z3. Warp and weft production: select 20 parts of cotton fiber, 6 parts of bamboo fiber, 15 parts of polyester fiber, 8 parts of superfine fiber, 12 parts of synthetic fiber and 20 parts of cupra fiber, and twist them as...
Embodiment 2
[0040] Z1. Select 40 parts of raw material elastic yarn, 17 parts of cashmere fiber, 8 parts of mulberry silk, 6 parts of chitosan fiber, 5 parts of anti-mold and mothproof agent, and 10 parts of silver fiber. After selection, 40 parts of elastic yarn , 17 parts of cashmere fiber and 10 parts of silver fiber are respectively opened and carded by fiber opening carding machine;
[0041] Z2. After combing, add it to the mixing mixer, continue to add 8 parts of mulberry silk, 6 parts of chitosan fiber, and 5 parts of anti-mold and mothproofing agent to the mixing mixer. After stirring for 12 minutes, they are dehydrated and dried. After slicing, spinning, winding, and stretching, the synthetic fiber is formed, and the diameter of the synthetic fiber is 65um;
[0042] Z3. Warp and weft production: select 25 parts of cotton fiber, 10 parts of bamboo fiber, 10 parts of polyester fiber, 10 parts of superfine fiber, 10 parts of synthetic fiber and 17 parts of cupra, and twist them as warp y...
Embodiment 3
[0047] Z1. Select 50 parts of raw material elastic yarn, 15 parts of cashmere fiber, 5 parts of mulberry silk, 5 parts of chitosan fiber, 3 parts of anti-mold and mothproof agent, 8 parts of silver fiber, and 50 parts of elastic yarn , 15 parts of cashmere fiber and 8 parts of silver fiber are respectively opened and carded by fiber opening carding machine;
[0048] Z2. After combing, add it to the mixing mixer, continue to add 5 parts of mulberry silk, 5 parts of chitosan fiber, and 3 parts of anti-mold and mothproofing agent to the mixing mixer. After stirring for 15 minutes, they are dehydrated and dried. After slicing, spinning, winding and stretching, the synthetic fiber is formed, and the diameter of the synthetic fiber is 70um;
[0049] Z3. Warp and weft production: select 30 parts of cotton fiber, 15 parts of bamboo fiber, 7 parts of polyester fiber, 6 parts of superfine fiber, 8 parts of synthetic fiber and 15 parts of cupra fiber, and twist them as warp threads 1 and lat...
PUM
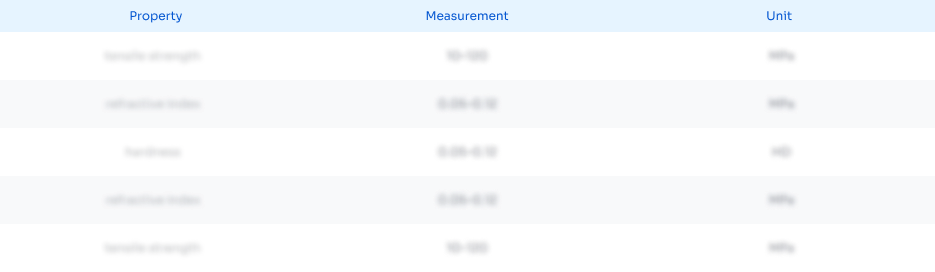
Abstract
Description
Claims
Application Information

- R&D
- Intellectual Property
- Life Sciences
- Materials
- Tech Scout
- Unparalleled Data Quality
- Higher Quality Content
- 60% Fewer Hallucinations
Browse by: Latest US Patents, China's latest patents, Technical Efficacy Thesaurus, Application Domain, Technology Topic, Popular Technical Reports.
© 2025 PatSnap. All rights reserved.Legal|Privacy policy|Modern Slavery Act Transparency Statement|Sitemap|About US| Contact US: help@patsnap.com