Solar sail driven to be unfolded by multi-steady-state curved beam intelligently
A multi-stable, curved beam technology, applied in the field of solar sails, can solve the problems of uncontrollable intermediate process, high energy consumption, poor stability, etc., and achieve the effect of zero Poisson's ratio, strong reliability and strong stability
- Summary
- Abstract
- Description
- Claims
- Application Information
AI Technical Summary
Problems solved by technology
Method used
Image
Examples
specific Embodiment approach 1
[0027] Specific implementation mode one: as Figure 1 to Figure 15 As shown, the present invention discloses a solar sail intelligently driven by a multi-stable curved beam, including a support shaft 12, an upper compression device 15, a lower compression device 16, four sail surfaces 14, and four extension arms 11. The four extension arms 11 are arranged in a cross shape with the support shaft 12 as the center, and the inner end of each extension arm 11 is hinged in the middle of the side wall of the support shaft 12. The extension arms 11 include several composite negative stiffness unit cells 1, the The composite negative stiffness unit cell 1 includes a curved beam structure 1-1 and three support structures 1-2, the curved beam structure 1-1 adopts shape memory polymer containing reinforced fibers, and the support structure 1-2 adopts nylon , the three support structures 1-2 are vertically fixed to the middle and both ends of the curved beam structure 1-1 respectively, and...
specific Embodiment approach 2
[0028] Specific implementation mode two: as figure 1 , 5 , 12, this embodiment is a further description of the specific embodiment 1, the plurality of composite negative stiffness unit cells 1 are in the unfolded state and are higher than the glass transition of the material of the curved beam structure 1-1 In the case of high temperature, it is compressed under the drive of external load to produce bending deformation for shaping. After the shape is shaped, it is naturally cooled and fixed to form the extension arm 11. When all the curved beam structures 1-1 of the extension arm 11 are heated to the same temperature at the same time Temperature, all the curved beam structures 1-1 return to the expanded state to release the prestress to make the extension arm 11 axially extend, the axial extension of the upper compression device 15 and the lower compression device 16 is the same as the axial extension of the extension arm 11.
specific Embodiment approach 3
[0029] Specific implementation mode three: as figure 1 As shown, this embodiment is a further description of the second embodiment. The two sides of the curved beam structure 1-1 use polyimide adhesive to paste the electric heating sheet on the initially expanded state containing reinforcing fibers. The inner surface of the shape-memory polymer is controlled by a temperature controller to control the temperature of the electric heating sheet, thereby changing the temperature of the curved beam structure 1-1.
PUM
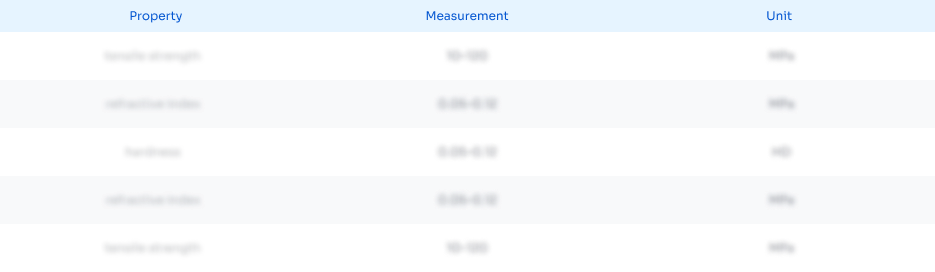
Abstract
Description
Claims
Application Information

- Generate Ideas
- Intellectual Property
- Life Sciences
- Materials
- Tech Scout
- Unparalleled Data Quality
- Higher Quality Content
- 60% Fewer Hallucinations
Browse by: Latest US Patents, China's latest patents, Technical Efficacy Thesaurus, Application Domain, Technology Topic, Popular Technical Reports.
© 2025 PatSnap. All rights reserved.Legal|Privacy policy|Modern Slavery Act Transparency Statement|Sitemap|About US| Contact US: help@patsnap.com