Rotating furnace smelting method with high steel scrap consumption
A converter smelting and steel scrap technology, which is applied in the field of iron and steel smelting, can solve the problems of increased production costs, large heat loss, and increased production costs, and achieve the effects of reducing steelmaking production costs, increasing TFe content, and alleviating market backlogs
- Summary
- Abstract
- Description
- Claims
- Application Information
AI Technical Summary
Problems solved by technology
Method used
Image
Examples
Embodiment 1
[0046] The indicators of steel material into the furnace are shown in Table 1:
[0047] Table 1
[0048]
[0049] According to the Si content of molten iron, the steel scrap ratio is determined to be 30%, and the content of iron ore in steel scrap accounts for 30%. Based on the steel scrap ratio of 10%, 13.3t of scrap steel and 6.7t of iron ore were added, and 20t of molten iron was reduced.
[0050] According to the heat balance formula:
[0051] Q 铁水化 =147.70*C%+269.70*Si%+70.00*Mn%+217.30*P%
[0052] =862.47(MJ / t)
[0053] Q 铁水物 =61.9+0.88*T
[0054] =1250(MJ / t)
[0055] Q 废钢化 =147.70*C%+269.70*Si%+70.00*Mn%+217.30*P%
[0056] =102.10(MJ / t)
[0057] Q 废钢物 =0.74T=14.8(MJ / t)
[0058] Q 铁矿石化 =147.70*C%+269.70*Si%+70.00*Mn%+217.30*P%
[0059] =920.03(MJ / t)
[0060] Q 铁矿石物 =0.74T=14.8(MJ / t)
[0061] Calculation by the heat balance formula can be seen in Table 2 as follows:
[0062] Table 2
[0063]
[0064] Calculation of added coke
[0065] The exother...
Embodiment 2
[0071] The indicators of the steel material into the furnace are shown in Table 3:
[0072] table 3
[0073]
[0074] According to the Si content of molten iron, the steel scrap ratio is determined to be 25%, and the content of iron ore in the steel scrap accounts for 33%. Based on the steel scrap ratio of 10%, 10t of scrap steel and 5t of iron ore are added, and 15t of molten iron is reduced.
[0075] According to the heat balance formula:
[0076] Q 铁水化 =147.70*C%+269.70*Si%+70.00*Mn%+217.30*P%
[0077] =822.02(MJ / t)
[0078] Q 铁水物 =61.9+0.88*T MJ / t
[0079] =1294(MJ / t)
[0080] Q 废钢化 =147.70*C%+269.70*Si%+70.00*Mn%+217.30*P%
[0081] =310.08(MJ / t)
[0082] Q 废钢物 =0.74T=14.8(MJ / t)
[0083] Q 铁矿石化 =147.70*C%+269.70*Si%+70.00*Mn%+217.30*P%
[0084] =920.03(MJ / t)
[0085] Q 铁矿石物 =0.74T=14.8(MJ / t)
[0086] Calculation by the heat balance formula can be seen in Table 4 as follows:
[0087] Table 4
[0088]
[0089] Add coke calculation
[0090] The exoth...
Embodiment 3
[0095] The indicators of the steel material into the furnace are shown in Table 5:
[0096] table 5
[0097]
[0098] According to the Si content of molten iron, the steel scrap ratio is determined to be 35%, and the content of iron ore in the steel scrap accounts for 35%. Based on the steel scrap ratio of 10%, steel scrap increased by 16.7t, iron ore by 8.3t, and molten iron decreased by 25t.
[0099] According to the heat balance formula:
[0100] Q 铁水化=147.70*C%+269.70*Si%+70.00*Mn%+217.30*P%
[0101] =902.93(MJ / t)
[0102] Q 铁水物 =61.9+0.88*T(MJ / t)
[0103] =1206(MJ / t)
[0104] Q 废钢化 =147.70*C%+269.70*Si%+70.00*Mn%+217.30*P%
[0105] =311.78(MJ / t)
[0106] Q 废钢物 =0.74T=14.8(MJ / t)
[0107] Q 铁矿石化 =147.70*C%+269.70*Si%+70.00*Mn%+217.30*P%
[0108] =920.03(MJ / t)
[0109] Q 铁矿石物 =0.74T=14.8(MJ / t)
[0110] The calorific value of the steel material entering the furnace calculated by the heat balance formula is shown in Table 6:
[0111] Table 6
[0112]
...
PUM
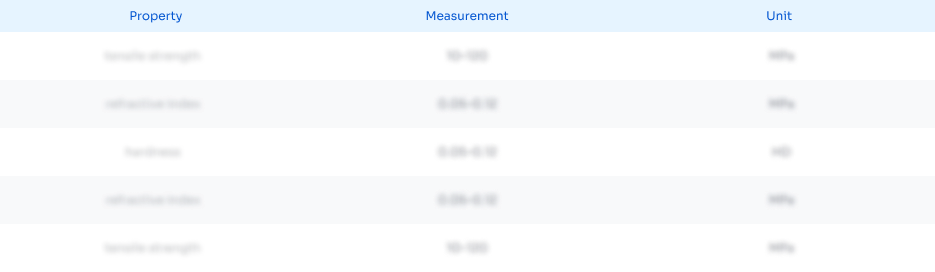
Abstract
Description
Claims
Application Information

- R&D
- Intellectual Property
- Life Sciences
- Materials
- Tech Scout
- Unparalleled Data Quality
- Higher Quality Content
- 60% Fewer Hallucinations
Browse by: Latest US Patents, China's latest patents, Technical Efficacy Thesaurus, Application Domain, Technology Topic, Popular Technical Reports.
© 2025 PatSnap. All rights reserved.Legal|Privacy policy|Modern Slavery Act Transparency Statement|Sitemap|About US| Contact US: help@patsnap.com