A Method for Optimizing the Charge Separation Efficiency of Carrier Conducting Layers
A charge separation and carrier technology, applied in coating, ion implantation plating, metal material coating process, etc., can solve the problems of unsuitability for industrialization, complexity, etc., to improve photoelectrochemical performance and high fault tolerance. , the effect of inhibiting electron-hole pair recombination
- Summary
- Abstract
- Description
- Claims
- Application Information
AI Technical Summary
Problems solved by technology
Method used
Image
Examples
Embodiment 1
[0025] The substrate (FTO glass) was ultrasonically cleaned, and the substrate was ultrasonically cleaned with acetone and absolute ethanol for 30 minutes respectively, and then sent into the sputtering chamber, and then the gate was opened to load until the vacuum degree (background vacuum degree) had reached 10 -4 In the deposition chamber below Pa. Oxygen and argon gas with a ratio of 1:6 were introduced, the total pressure was controlled to be 1Pa, and the distance between the target and the substrate was 8cm, and the carrier transport layer was deposited. Sputtering pure Sn target material, deposition time 5min. After the deposition is complete, the sample tray is sent into the etch deposition chamber. First draw the local vacuum down to below 5 Pa. The transparent conductive substrate was etched by direct current plasma, the atmosphere was high-purity argon, the gas flow rate was 100 sccm, the gas pressure was 10 Pa, the distance between the electrode and the substrat...
Embodiment 2
[0027] The substrate (FTO glass) was ultrasonically cleaned, and the substrate was ultrasonically cleaned with acetone and absolute ethanol for 30 minutes respectively, and then sent into the sputtering chamber, and then the gate was opened to load until the vacuum degree (background vacuum degree) had reached 10 -4 In the deposition chamber below Pa Pa. Oxygen and argon gas with a ratio of 1:6 were introduced, the total pressure was controlled to be 1Pa, and the distance between the target and the substrate was 8cm, and the carrier transport layer was deposited. The pure Ti target is sputtered, and the deposition time is 15 minutes. After the deposition is complete, the sample tray is sent into the etch deposition chamber. First draw the local vacuum down to below 5 Pa. The transparent conductive substrate was etched by direct current plasma, the atmosphere was high-purity argon, the gas flow rate was 100 sccm, the gas pressure was 10 Pa, the distance between the electrode...
Embodiment 3
[0029] The substrate (FTO glass) was ultrasonically cleaned, and the substrate was ultrasonically cleaned with acetone and absolute ethanol for 30 minutes respectively, and then sent into the sputtering chamber, and then the gate was opened to load until the vacuum degree (background vacuum degree) had reached 10 -4 In the deposition chamber below Pa Pa. Oxygen and argon gas with a ratio of 1:6 were introduced, the total pressure was controlled to be 1Pa, and the distance between the target and the substrate was 8cm, and the carrier transport layer was deposited. Sputtering pure Sn target material, deposition time 5min. After the deposition is complete, the sample tray is sent into the etch deposition chamber. First draw the local vacuum down to below 5 Pa. The transparent conductive substrate was etched by direct current plasma, the atmosphere was high-purity argon, the gas flow rate was 100 sccm, the gas pressure was 10 Pa, the distance between the electrode and the subst...
PUM
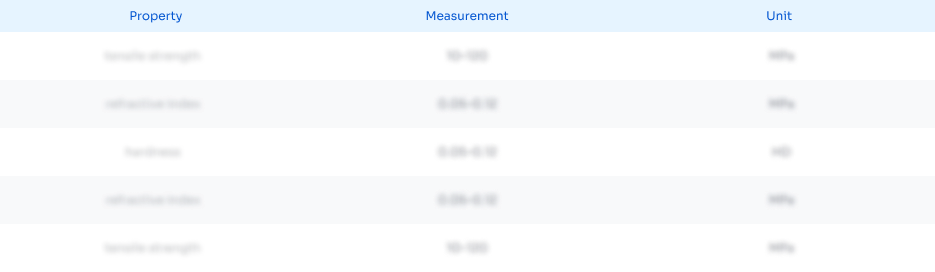
Abstract
Description
Claims
Application Information

- Generate Ideas
- Intellectual Property
- Life Sciences
- Materials
- Tech Scout
- Unparalleled Data Quality
- Higher Quality Content
- 60% Fewer Hallucinations
Browse by: Latest US Patents, China's latest patents, Technical Efficacy Thesaurus, Application Domain, Technology Topic, Popular Technical Reports.
© 2025 PatSnap. All rights reserved.Legal|Privacy policy|Modern Slavery Act Transparency Statement|Sitemap|About US| Contact US: help@patsnap.com