A kind of anti-aging polyester composite material and preparation method thereof
A polyester composite material and anti-aging technology, applied in the field of materials science, can solve the problems of low molecular weight and poor toughness of PLA, and achieve good interaction, excellent anti-ultraviolet aging performance, and high rigidity
- Summary
- Abstract
- Description
- Claims
- Application Information
AI Technical Summary
Problems solved by technology
Method used
Image
Examples
Embodiment 1
[0033] 1. Preparation of nanoparticles modified by reactive elastomer macromolecules:
[0034] (1) first nano-TiO 2 Disperse the dispersant polyvinylpyrrolidone in the ethanol / deionized water mixture, control the pH of the system to about 9, slowly drop into the ethanol solution of tetraethyl orthosilicate, fully react at room temperature, and finally separate and obtain coated SiO 2 layer of nanoparticles (TiO 2 @SiO 2 );
[0035] (2) Secondly, the silane coupling agent KH550 is hydrolyzed in deionized water to obtain a homogeneous solution, and then a certain amount of TiO 2 @SiO 2 Nanoparticles were added into the solution, fully reacted at 70 ° C, and finally separated to obtain nanoparticles modified by silane coupling agent (TiO 2 @SiO 2 -KH550), wherein the silane coupling agent KH550 quality is TiO 2 @SiO 2 1.5 times the mass;
[0036] (3) the TiO obtained above 2 @SiO 2 -KH550 nanoparticles are added to N,N-dimethylformamide, then epoxidized vinyl acetate-b...
Embodiment 2
[0041] 1. Preparation of nanoparticles modified by reactive elastomer macromolecules:
[0042] TiO in embodiment 1 2 Replaced by ZnO, the same method was used to prepare nanoparticles modified by reactive elastomeric macromolecules to obtain ZnO@SiO 2 - g-epoxidized vinyl acetate based copolymer.
[0043] 2. Preparation of composite materials:
[0044] 80 parts of PBT, 20 parts of ethylene-vinyl acetate-glycidyl methacrylate copolymer (the mass content of vinyl acetate is 60%, the mass content of glycidyl methacrylate is 3%), ZnO@SiO 2 -1 part of g-epoxidized vinyl acetate-based copolymer and functional additives were added to the internal mixer for melt blending for 5 minutes (blending temperature was 235°C, rotation speed was 80rpm) to obtain a high-toughness anti-ultraviolet aging PBT composite material.
[0045] The above-mentioned high-toughness and anti-ultraviolet aging PBT composite material was hot-pressed by a flat vulcanizer for tensile, impact performance and u...
Embodiment 3
[0047] 1. Preparation of nanoparticles modified by reactive elastomer macromolecules:
[0048] Adopt the same method of embodiment 1 to prepare the nanoparticle TiO of reactive elastomer macromolecule modification 2 @SiO 2 - g-epoxidized vinyl acetate based copolymer.
[0049] 2. Preparation of composite materials:
[0050] Will reclaim PET75 parts, ethylene-vinyl acetate-glycidyl methacrylate copolymer (vinyl acetate mass content is 60%, glycidyl methacrylate mass content is 3%) 25 parts, TiO 2 @SiO 2 - 1 part of epoxidized vinyl acetate-based copolymer is premixed uniformly at room temperature, and then the premix is added to the conveying section of the twin-screw extruder, and is continuously melted and extruded (extrusion temperature is 260 ° C, screw speed Be 180rpm) obtain a kind of high tenacity anti-ultraviolet aging PET composite material.
[0051] The extruded high-toughness anti-ultraviolet aging PET composite material was fully dried and then injected into ...
PUM
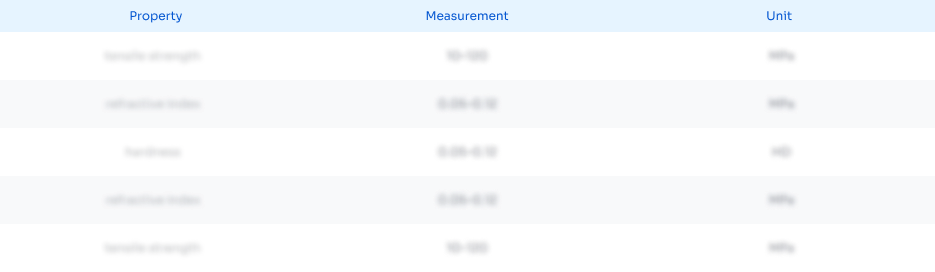
Abstract
Description
Claims
Application Information

- Generate Ideas
- Intellectual Property
- Life Sciences
- Materials
- Tech Scout
- Unparalleled Data Quality
- Higher Quality Content
- 60% Fewer Hallucinations
Browse by: Latest US Patents, China's latest patents, Technical Efficacy Thesaurus, Application Domain, Technology Topic, Popular Technical Reports.
© 2025 PatSnap. All rights reserved.Legal|Privacy policy|Modern Slavery Act Transparency Statement|Sitemap|About US| Contact US: help@patsnap.com