Vision-based automatic stacking system and method
A palletizing system and automatic technology, applied in the field of vision-based automatic palletizing systems, can solve problems such as poor flexibility and complicated changes, and achieve the effect of high picking success rate, high level of intelligence, and high degree of automation
- Summary
- Abstract
- Description
- Claims
- Application Information
AI Technical Summary
Problems solved by technology
Method used
Image
Examples
Embodiment 1
[0033] see Figure 1-3 , the present invention provides a technical solution: a vision-based automatic palletizing system and method, including an automatic package supply line (1), a photoelectric sensor (2), a target object (3), a bracket (4), and a palletizing subsystem , vision system, secondary positioning subsystem, it is characterized in that: described secondary positioning subsystem comprises secondary positioning light source (10) and secondary positioning camera (11); Described stacking subsystem comprises robot (7), terminal Executor (8), fixed frame (9), pallet (12) and secondary positioning subsystem; the vision system includes identification and positioning light source (4), identification and positioning camera (5) and secondary positioning subsystem;
[0034] The robot (7) is a six-degree-of-freedom robot located on the side of the automatic bag supply line (1); the robot (7) is located behind the support (6) along the direction of the conveyor belt; the end e...
Embodiment 2
[0051] When the size of the target object varies in a large range or has many types, a group of robots and end effectors are not competent. At this time, two or more palletizing subsystems can be arranged on both sides of the automatic bag supply line. Refer to the attached Figure 4 Be specific.
[0052] An automatic palletizing system based on visual positioning, refer to the attached Figure 4 , including automatic package supply line 1, photoelectric sensor 2, target object 3, bracket 6, vision system, palletizing subsystem A, palletizing subsystem B, secondary positioning subsystem A, secondary positioning subsystem B.
[0053] The secondary positioning subsystem A includes a secondary positioning light source 10A and a secondary positioning camera 11A; the palletizing subsystem A includes a robot 7A, an end effector 8A, a fixed frame 9A, a pallet 12A and a secondary positioning subsystem A The secondary positioning subsystem B includes a secondary positioning light so...
PUM
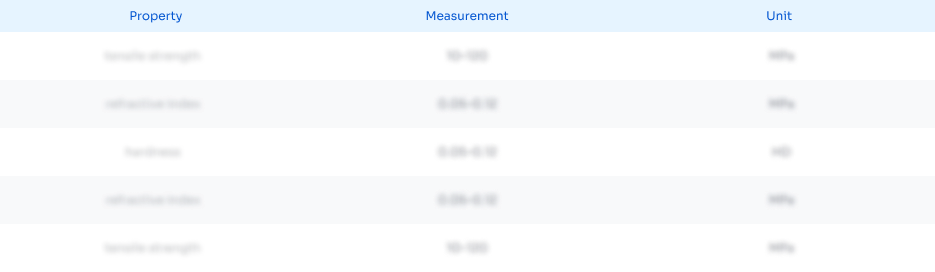
Abstract
Description
Claims
Application Information

- R&D
- Intellectual Property
- Life Sciences
- Materials
- Tech Scout
- Unparalleled Data Quality
- Higher Quality Content
- 60% Fewer Hallucinations
Browse by: Latest US Patents, China's latest patents, Technical Efficacy Thesaurus, Application Domain, Technology Topic, Popular Technical Reports.
© 2025 PatSnap. All rights reserved.Legal|Privacy policy|Modern Slavery Act Transparency Statement|Sitemap|About US| Contact US: help@patsnap.com