Method for eliminating surface defects of carbon steel intermediate blank
A technology for carbon steel and defects, which is applied in the field of eliminating surface defects of carbon steel intermediate blanks, can solve the problems of unconsidered cost and workshop environmental pollution, increase the amount of grinding, and reduce the amount of grinding, so as to reduce the surface defects of the substrate and reduce the Effects of dust generation and billet defect improvement
- Summary
- Abstract
- Description
- Claims
- Application Information
AI Technical Summary
Problems solved by technology
Method used
Image
Examples
Embodiment Construction
[0020] Below in conjunction with embodiment the present invention is further described in detail.
[0021] The method for eliminating the surface defect of the carbon steel intermediate billet in the present invention adopts air cooling-slow cooling in the heat preservation channel-air cooling to room temperature-shot blasting-magnetic particle flaw detection-defect spot grinding treatment, including the following steps:
[0022] (1) Treatment of the intermediate slab after billet rolling: the continuous casting slab is rolled at 1080-1150°C to produce an intermediate billet with a size of 140×140mm-160×160mm, and the intermediate billet is air-cooled-slowly cooled in a heat preservation channel -Air-cooling to room temperature, the temperature of the upper cooling bed of the intermediate billet is ≥1055°C, the temperature entering the heat preservation channel is controlled at 1000±10°C, the temperature at the exit of the heat preservation channel is 900±10°C, and the average ...
PUM
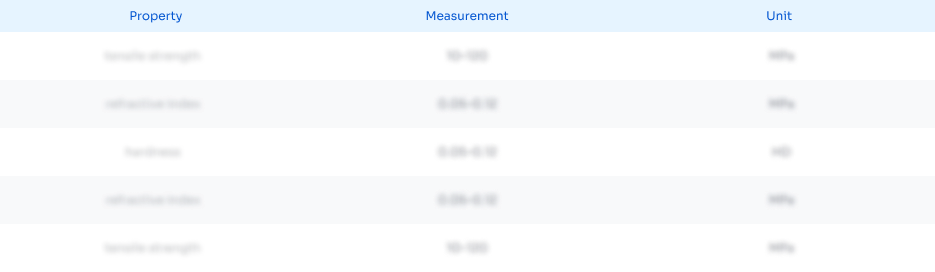
Abstract
Description
Claims
Application Information

- R&D
- Intellectual Property
- Life Sciences
- Materials
- Tech Scout
- Unparalleled Data Quality
- Higher Quality Content
- 60% Fewer Hallucinations
Browse by: Latest US Patents, China's latest patents, Technical Efficacy Thesaurus, Application Domain, Technology Topic, Popular Technical Reports.
© 2025 PatSnap. All rights reserved.Legal|Privacy policy|Modern Slavery Act Transparency Statement|Sitemap|About US| Contact US: help@patsnap.com