Reaction equipment and method for preparing alkylated gasoline by sulfuric acid alkylation process
A technology of alkylated gasoline and reaction device, applied in chemical instruments and methods, chemical/physical/physical-chemical stationary reactors, chemical/physical/physical-chemical processes, etc., can solve the problem of reducing product quality and increasing reactor size Processing difficulty and cost, increasing internal side reactions, etc., to achieve the effect of increasing the contact area between the phases, overcoming the low reaction efficiency and improving the reaction rate
- Summary
- Abstract
- Description
- Claims
- Application Information
AI Technical Summary
Problems solved by technology
Method used
Image
Examples
Embodiment 1
[0061] use as figure 1 The reactor shown carries out the alkylation reaction. Feed isobutane and 2-butene at a molar ratio of 10:1, raise the system pressure to 0.25 Mpa, then feed 98.7% concentrated sulfuric acid from another feed pipe, the volume ratio of concentrated sulfuric acid to mixed hydrocarbons is 1:1, two streams of materials are ejected from the nozzle, and enter the upper and lower layers of packing after impact, control the packing speed at 550 rpm, and control the reaction temperature at 15°C. The material thrown out from the lower layer of filler enters the guide tube for reforming reaction. The rotation speed of the stirring paddle is the same as that of the filler. After the reaction is completed, the material flows out from the liquid outlet. The resulting product had zero olefin content and an octane number of 94.8 (research octane number).
Embodiment 2
[0063] use as figure 1 The reactor shown carries out the alkylation reaction. Feed isobutane and 2-butene at a molar ratio of 10:1, raise the system pressure to 0.17 Mpa, then feed 98.7% concentrated sulfuric acid from another feed pipe, the volume ratio of concentrated sulfuric acid to mixed hydrocarbons is 1:1, two streams of materials are ejected from the nozzle, and enter the upper and lower layers of packing after impact, the packing speed is controlled at 1000 rpm, and the reaction temperature is controlled at 6°C. The material thrown out from the lower layer of filler enters the guide tube for reforming reaction. The rotation speed of the stirring paddle is the same as that of the filler. After the reaction is completed, the material flows out from the liquid outlet. The olefin content in the obtained product was 0, and the octane number was 97.5. (Research Octane Number)
Embodiment 3
[0065] use as figure 1 The reactor shown carries out the alkylation reaction. Feed isobutane and 2-butene at a molar ratio of 8:1, raise the system pressure to 0.15 Mpa, and then feed 98.7% concentrated sulfuric acid from another feed pipe, the volume ratio of concentrated sulfuric acid to mixed hydrocarbons is 1:1, two streams of materials are ejected from the nozzle, and enter the upper and lower layers of packing after impact, the filling speed is controlled at 1500 rpm, and the reaction temperature is controlled at 0°C. The material thrown out from the lower layer of filler enters the guide tube for reforming reaction. The rotation speed of the stirring paddle is the same as that of the filler. After the reaction is completed, the material flows out from the liquid outlet. The olefin content in the obtained product was 0, and the octane number was 98.6. (Research Octane Number)
PUM
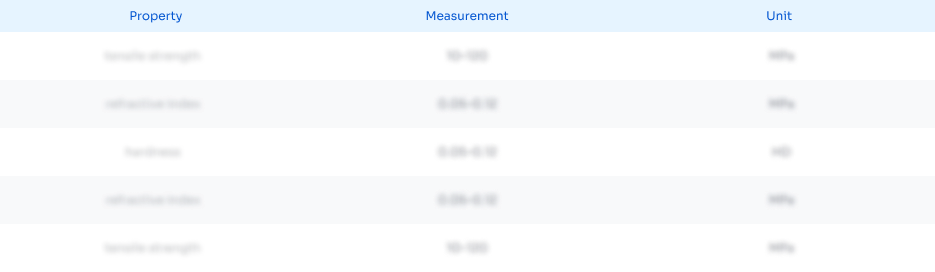
Abstract
Description
Claims
Application Information

- R&D
- Intellectual Property
- Life Sciences
- Materials
- Tech Scout
- Unparalleled Data Quality
- Higher Quality Content
- 60% Fewer Hallucinations
Browse by: Latest US Patents, China's latest patents, Technical Efficacy Thesaurus, Application Domain, Technology Topic, Popular Technical Reports.
© 2025 PatSnap. All rights reserved.Legal|Privacy policy|Modern Slavery Act Transparency Statement|Sitemap|About US| Contact US: help@patsnap.com