Wood-plastic composite foaming material and preparation method thereof
A foam material and wood-plastic composite technology, applied in the field of composite materials, can solve problems affecting product sales, high production costs, toxic substances, etc., and achieve the effects of avoiding toxic substances from harming human health, low cost, and high transparency
- Summary
- Abstract
- Description
- Claims
- Application Information
AI Technical Summary
Problems solved by technology
Method used
Image
Examples
Embodiment 1
[0035] (1) Bake the corn stalk powder at 120 degrees centigrade for 4 hours to keep the moisture content below 3.5%.
[0036] (2) In parts by weight, weigh 20 parts of corn stalk powder, 30 parts of waste plastics, 10 parts of alumina fiber, 13-15 parts of fluorite, 2 parts of foaming material, 3 parts of antioxidant, 4 parts of stabilizer, 40 parts of silica, 7 parts of impact modifier, 8 parts of processing aid, 1 part of auxiliary stabilizer and 2 parts of lubricant.
[0037] (3) According to processing step 1: add the above-mentioned raw materials into a high-speed mixer, and stir at a speed of 50-80r / min for 8-10min at room temperature;
[0038] Step 2: stirring at 100-115°C and 70-100r / min for 15-30min to obtain a premix;
[0039] Step 3: Put the premixed material obtained in Step 2 into a kneader, melt it, and after cooling, crush it into granules or powders with a particle size below 1mm for use;
[0040] Step 4: The wood-plastic composite foam material is obtained b...
Embodiment 2
[0042] (1) Bake the corn stalk powder for 4 hours at 100°C to keep the moisture content below 3.5%.
[0043] (2) In parts by weight, weigh 30 parts of corn stalk powder, 40 parts of waste plastics, 11 parts of alumina fiber, 14 parts of fluorite, 3 parts of foaming material, 4 parts of antioxidant, 5 parts of stabilizer, two 50 parts of silicon oxide, 8 parts of impact modifier, 9 parts of processing aid, 2 parts of auxiliary stabilizer and 4 parts of lubricant.
[0044] (3) According to processing step 1: add the above-mentioned raw materials into a high-speed mixer, and stir at a speed of 50-80r / min for 8-10min at room temperature;
[0045] Step 2: stirring at 100-115°C and 70-100r / min for 15-30min to obtain a premix;
[0046] Step 3: Put the premixed material obtained in Step 2 into a kneader, melt it, and after cooling, crush it into granules or powders with a particle size below 1mm for use;
[0047] Step 4: The wood-plastic composite foam material is obtained by inject...
Embodiment 3
[0049] (1) Bake the corn stalk powder for 4 hours at 100°C to keep the moisture content below 3.5%.
[0050] (2) In parts by weight, weigh 40 parts of corn stalk powder, 50 parts of waste plastics, 12 parts of alumina fiber, 15 parts of fluorite, 4 parts of foaming material, 5 parts of antioxidant, 6 parts of stabilizer, two 60 parts of silicon oxide, 9 parts of impact modifier, 10 parts of processing aid, 3 parts of auxiliary stabilizer and 5 parts of lubricant.
[0051] (3) According to processing step 1: add the above-mentioned raw materials into a high-speed mixer, and stir at a speed of 50-80r / min for 8-10min at room temperature;
[0052] Step 2: stirring at 100-115°C and 70-100r / min for 15-30min to obtain a premix;
[0053] Step 3: Put the premixed material obtained in Step 2 into a kneader, melt it, and after cooling, crush it into granules or powders with a particle size below 1mm for use;
[0054] Step 4: The wood-plastic composite foam material is obtained by injec...
PUM
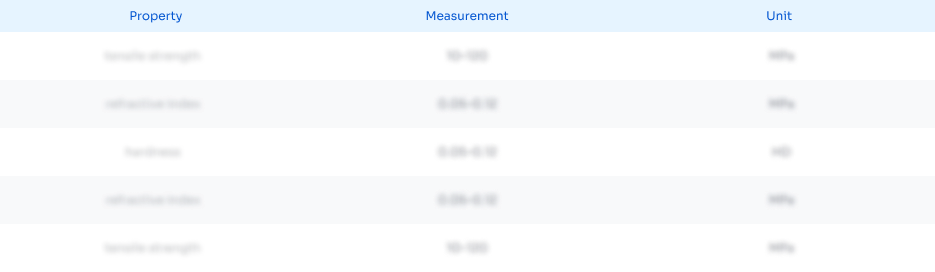
Abstract
Description
Claims
Application Information

- R&D
- Intellectual Property
- Life Sciences
- Materials
- Tech Scout
- Unparalleled Data Quality
- Higher Quality Content
- 60% Fewer Hallucinations
Browse by: Latest US Patents, China's latest patents, Technical Efficacy Thesaurus, Application Domain, Technology Topic, Popular Technical Reports.
© 2025 PatSnap. All rights reserved.Legal|Privacy policy|Modern Slavery Act Transparency Statement|Sitemap|About US| Contact US: help@patsnap.com