Motor shaft forging normalizing and tempering process
A technology for motor shafts and forgings, which is applied in the field of normalizing and tempering technology for motor shaft forgings, which can solve the problems of reducing the pace of power station construction, long construction period, and lack of economic benefits, so as to shorten heat treatment time and improve production efficiency effect
- Summary
- Abstract
- Description
- Claims
- Application Information
AI Technical Summary
Problems solved by technology
Method used
Image
Examples
Embodiment Construction
[0021] refer to figure 1 According to the normalizing and tempering process of motor shaft forgings of the present invention, the motor shaft forgings with a radius of 400mm are normalized and tempered. S001: Use carbon-manganese steel ingots smelted by electric arc furnace, refined outside the furnace, and smelted by vacuum degassing as raw materials for motor shaft forgings. During the above refining and smelting process, ensure that in the motor shaft forgings: S≤0.020%, P≤0.015 %, H≤2ppm, O≤30ppm, N≤65ppm, Cu≤0.20%. S002: After the motor shaft forging is fully austenitized, it is cooled to 320±20°C by air cooling or water mist, and then the motor shaft forging is placed in a heat treatment furnace for heat preservation at 200mm / h to reach the internal and external temperature of the motor shaft forging Consistent, the transformation of pearlite structure is completed. Since the radius of the motor shaft forging is 400mm, the above holding time is 2 hours. S003: The motor...
PUM
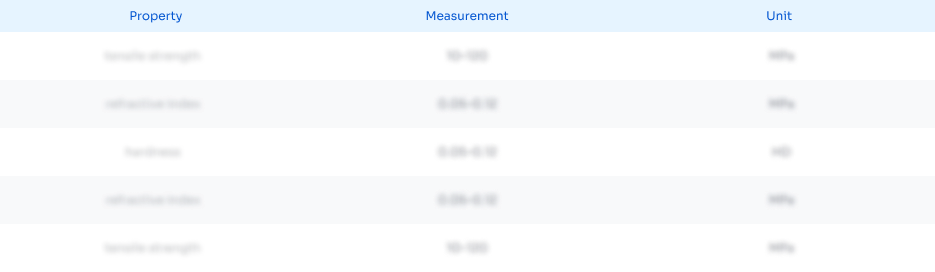
Abstract
Description
Claims
Application Information

- R&D Engineer
- R&D Manager
- IP Professional
- Industry Leading Data Capabilities
- Powerful AI technology
- Patent DNA Extraction
Browse by: Latest US Patents, China's latest patents, Technical Efficacy Thesaurus, Application Domain, Technology Topic, Popular Technical Reports.
© 2024 PatSnap. All rights reserved.Legal|Privacy policy|Modern Slavery Act Transparency Statement|Sitemap|About US| Contact US: help@patsnap.com