Processing technology of metal strip for assembling iron core of electronic transformer
An electronic transformer and processing technology, applied in metal processing equipment, circuits, electrical components, etc., can solve the problem of high scrap rate, achieve the effect of reducing scrap rate, good quenching and tempering effect, and improving flexibility
- Summary
- Abstract
- Description
- Claims
- Application Information
AI Technical Summary
Problems solved by technology
Method used
Image
Examples
Embodiment 1
[0019] The metal strip processing technology for electronic transformer core assembly includes the following steps:
[0020] (1) Ingredients: Weigh each raw material according to the silicon steel strip formula: 94.3% iron, 5.0% silicon, 0.2% boron, 0.3% copper, 0.2% nickel, the sum of the contents of each component is 100%;
[0021] (2) Smelting: Add the raw materials into the intermediate frequency induction furnace in the order of iron, nickel, silicon, copper, and boron according to the specific gravity of the ingredients for smelting. As the furnace heats up, the maximum melting temperature is 1600°C. After holding for 2 hours, vacuumize for 10 minutes , cooled to 800°C by water to obtain a smelted block;
[0022] (3) Secondary melting: Put the primary smelting block processed in step (2) into another intermediate frequency induction furnace for secondary melting. The temperature of the secondary melting is 1400°C. After holding for 2 hours, vacuumize for 10 minutes to ob...
Embodiment 2
[0027] The metal strip processing technology for electronic transformer core assembly includes the following steps:
[0028] (1) Ingredients: Weigh each raw material according to the silicon steel strip formula: 95.8% iron, 3.5% silicon, 0.25% boron, 0.2% copper, 0.25% nickel, the sum of the contents of each component is 100%;
[0029] (2) Smelting: Add the raw materials into the intermediate frequency induction furnace in the order of iron, nickel, silicon, copper, and boron according to the specific gravity of the ingredients, and then smelt them. As the furnace heats up, the maximum melting temperature is 1500°C. After holding for 1 hour, vacuumize for 5 minutes. , cooled to 700°C by water to obtain a smelted block;
[0030] (3) Secondary melting: Put the primary smelting block processed in step (2) into another intermediate frequency induction furnace for secondary melting. The temperature of the secondary melting is 1300°C. After holding for 1 hour, vacuumize for 5 minute...
PUM
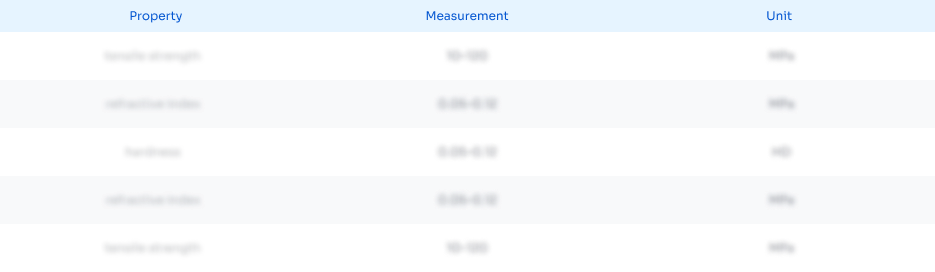
Abstract
Description
Claims
Application Information

- R&D
- Intellectual Property
- Life Sciences
- Materials
- Tech Scout
- Unparalleled Data Quality
- Higher Quality Content
- 60% Fewer Hallucinations
Browse by: Latest US Patents, China's latest patents, Technical Efficacy Thesaurus, Application Domain, Technology Topic, Popular Technical Reports.
© 2025 PatSnap. All rights reserved.Legal|Privacy policy|Modern Slavery Act Transparency Statement|Sitemap|About US| Contact US: help@patsnap.com