Closed rotary control system and crane
A control system and crane technology, applied in cranes, fluid pressure actuation system components, mechanical equipment, etc., can solve the problems of rapid oil temperature rise, large amount of calculation, poor stability, etc.
- Summary
- Abstract
- Description
- Claims
- Application Information
AI Technical Summary
Problems solved by technology
Method used
Image
Examples
Embodiment 1
[0065] In some embodiments, such as figure 1 As shown, a closed rotary control system includes: an electronically controlled variable pump 1, a pump displacement swing angle control valve 2, a pump displacement swing angle sensor 3, a swing motor 4, a swing speed sensor 6, a state information module 9, Accelerator pedal 13, joystick 14, buffer pedal 15, dynamic brake 5, dynamic buffer control valve 8, pilot system 11, force limit controller 10, free slip control valve 7, crane controller 12;
[0066] The accelerator pedal 13, joystick 14, buffer pedal 15, pump displacement swing angle sensor 3, and slewing speed sensor 6 are respectively connected to the signal input end of the crane controller 12, and the signal output end of the crane controller 12 is connected to the pilot system 11;
[0067] The state information module 9 of the crane is connected to the signal input end of the force limit controller 10, and the signal output end of the force limit controller 10 is respect...
Embodiment 2
[0072] A closed slewing control method, comprising:
[0073] Such as figure 1 and figure 2As shown, when the operator manipulates the handle to rotate, the force limit controller 10 obtains the current state information of the crane, determines the working condition parameters such as the hoisting weight, luffing angle, and outrigger length, and transmits them to the crane controller , the crane controller obtains the corresponding handle angle change rate preset value according to the current working condition parameters. For example, the handle angle change rate preset value is 0.01° / ms when a certain working condition parameter The handle angle change information is calculated to obtain the actual change rate of the current handle angle. If the actual change rate of the current handle angle exceeds 0.01° / ms, the force limit controller 10 controls the change process of the current input to the pump displacement swing angle control valve 2. Compensation control, so that th...
PUM
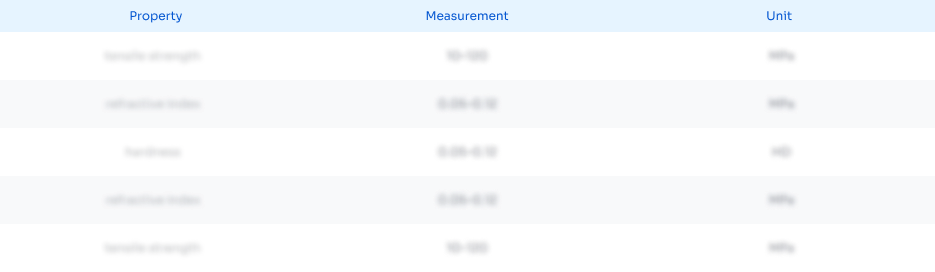
Abstract
Description
Claims
Application Information

- R&D
- Intellectual Property
- Life Sciences
- Materials
- Tech Scout
- Unparalleled Data Quality
- Higher Quality Content
- 60% Fewer Hallucinations
Browse by: Latest US Patents, China's latest patents, Technical Efficacy Thesaurus, Application Domain, Technology Topic, Popular Technical Reports.
© 2025 PatSnap. All rights reserved.Legal|Privacy policy|Modern Slavery Act Transparency Statement|Sitemap|About US| Contact US: help@patsnap.com