Clamping mechanism for grinding and polishing robot system for high-temperature alloy mechanical parts of engine
A robotic system and superalloy technology, which is used in grinding machine parts, grinding/polishing equipment, grinding machines, etc., to solve problems such as insufficient support force, easy slippage during grinding and polishing, and damage to engine alloy components.
- Summary
- Abstract
- Description
- Claims
- Application Information
AI Technical Summary
Problems solved by technology
Method used
Image
Examples
Embodiment Construction
[0026] The embodiment of the present application solves the problems raised in the prior art by providing a clamping mechanism for the grinding and polishing robot system of the superalloy mechanism of the engine; the following will be clearly and completely described in conjunction with the technical solution in the embodiment of the present invention, Apparently, the described embodiments are only some of the embodiments of the present invention, but not all of them. Based on the embodiments of the present invention, all other embodiments obtained by persons of ordinary skill in the art without making creative efforts belong to the protection scope of the present invention.
[0027] see Figure 1-4 , this embodiment provides a clamping mechanism for a grinding and polishing robot system for high-temperature alloy parts of an engine, including a workbench 1 and a data processing module 15 embedded in the inner cavity of the workbench 1, and the left and right sides of the top...
PUM
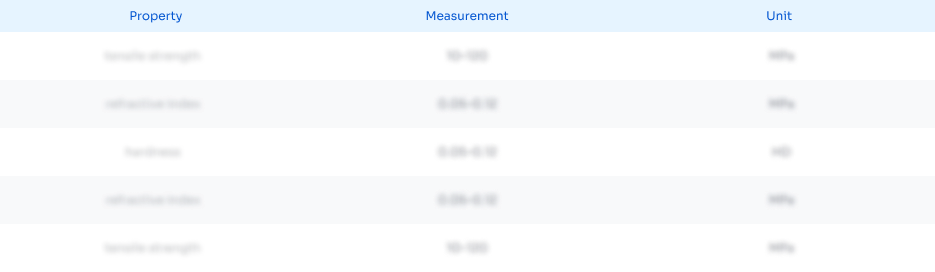
Abstract
Description
Claims
Application Information

- R&D
- Intellectual Property
- Life Sciences
- Materials
- Tech Scout
- Unparalleled Data Quality
- Higher Quality Content
- 60% Fewer Hallucinations
Browse by: Latest US Patents, China's latest patents, Technical Efficacy Thesaurus, Application Domain, Technology Topic, Popular Technical Reports.
© 2025 PatSnap. All rights reserved.Legal|Privacy policy|Modern Slavery Act Transparency Statement|Sitemap|About US| Contact US: help@patsnap.com