Sintering process ore blending optimization method
An optimization method and technology of sintering process, applied in chemical process analysis/design, genetic rules, special data processing application, etc., can solve the problem that ore blending technology relies on manual expert experience, does not consider the properties of mixed ore, etc., to reduce sintering cost , reduce business capabilities, and reduce the effect of data loss
- Summary
- Abstract
- Description
- Claims
- Application Information
AI Technical Summary
Problems solved by technology
Method used
Image
Examples
Embodiment 1
[0039] Combine below figure 1 , taking the actual situation of a sintering plant as an example, the specific implementation of the present invention is described in detail.
[0040] The sintering process ore distribution optimization method of the present embodiment includes the following steps:
[0041] Step 1: Collect historical data of various physical and chemical indicators of the mixed ore, including total iron grade (TFe), alkalinity (Ro), calcium oxide value (CaO), silicon dioxide value (SiO 2 ), magnesium oxide value (MgO); see Table 1 for historical data of mixed ore;
[0042] Table 1 Historical data of physical and chemical indicators of mixed ore
[0043]
[0044]
[0045] Step 2: Collect historical data of sinter properties corresponding to the mixed ore, including total iron grade, alkalinity, iron oxide value, silica value, calcium oxide value, magnesium oxide value, first-grade product rate, qualified product rate; sintering The historical data of the ...
PUM
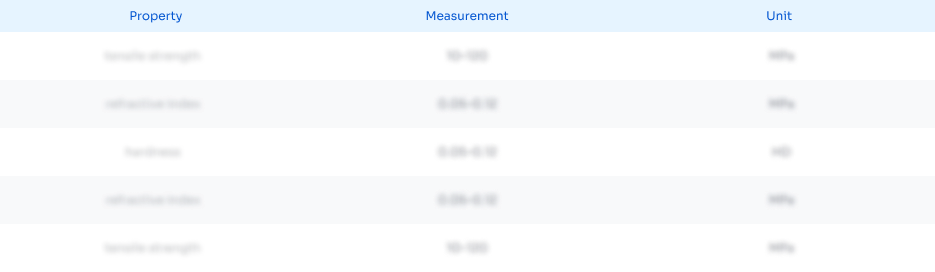
Abstract
Description
Claims
Application Information

- R&D
- Intellectual Property
- Life Sciences
- Materials
- Tech Scout
- Unparalleled Data Quality
- Higher Quality Content
- 60% Fewer Hallucinations
Browse by: Latest US Patents, China's latest patents, Technical Efficacy Thesaurus, Application Domain, Technology Topic, Popular Technical Reports.
© 2025 PatSnap. All rights reserved.Legal|Privacy policy|Modern Slavery Act Transparency Statement|Sitemap|About US| Contact US: help@patsnap.com