Method for synergistically toughening ceramic material by graphene and nano zirconia and application thereof
A technology of nano-zirconia and toughened ceramics, which is applied in the field of ceramic tool materials, can solve the problems of microhardness and fracture toughness reduction, and achieve the effects of improving compactness, inhibiting growth, and improving fracture toughness
- Summary
- Abstract
- Description
- Claims
- Application Information
AI Technical Summary
Problems solved by technology
Method used
Image
Examples
Embodiment 1
[0033] A method for synergistically toughening ceramic materials with graphene and nano-zirconia, comprising the steps of:
[0034] (1) Ultrasonic dispersion of graphene and nano-zirconia in an anhydrous ethanol medium for 2 hours to prepare a suspension with a mass fraction of graphene of 0.4% and a mass fraction of nano-zirconia of 1%;
[0035] (2) the powder of 47.72% aluminum oxide, 50.33% titanium carbonitride, 0.49% magnesium oxide, 0.06% yttrium oxide and the suspension (remainder) of graphene and nano-zirconia that step (1) obtains by mass fraction ) were added together in the ball mill cylinder, the ball mill balls were wear-resistant alumina balls, and the high-energy ball milled for 48 hours to obtain the mixture;
[0036] (3) Dry the mixture after ball milling in step (2) in a vacuum oven at a temperature of 120° C. for 1.5 hours; pass through a 150-mesh sieve after drying;
[0037] (4) Put the composite raw material powder sieved in step (3) into a graphite mold,...
Embodiment 2
[0039] A method for synergistically toughening ceramic materials with graphene and nano-zirconia, comprising the steps of:
[0040] (1) Ultrasonic dispersion of graphene and nano-zirconia in anhydrous ethanol medium for 2.5 hours, to prepare a suspension with a mass fraction of graphene of 1.2% and a mass fraction of nano-zirconia of 0.5%;
[0041] (2) the powder of 46.96% aluminum oxide, 51.23% titanium carbonitride, 0.53% magnesium oxide, 0.08% yttrium oxide and the suspension (remainder) of graphene and nano-zirconia that step (1) obtains by mass fraction ) are added together in the ball mill cylinder, the ball mill balls are wear-resistant alumina balls, and the high-energy ball mill is used for 60 hours to obtain the mixture;
[0042] (3) Dry the mixture after ball milling in step (2) in a vacuum oven at a temperature of 100° C. for 2 hours; pass through a 120-mesh sieve after drying;
[0043](4) Put the composite raw material powder sieved in step (3) into a graphite mo...
Embodiment 3
[0045] A method for synergistically toughening ceramic materials with graphene and nano-zirconia, comprising the steps of:
[0046] (1) Ultrasonic dispersion of graphene and nano-zirconia in anhydrous ethanol medium for 2 hours to prepare a suspension with a mass fraction of graphene of 0.2% and a mass fraction of nano-zirconia of 2.0%;
[0047] (2) the powder of 47.16% aluminum oxide, 50.29% titanium carbonitride, 0.45% magnesium oxide, 0.1% yttrium oxide and the suspension (remainder) of graphene and nano-zirconia that step (1) obtains by mass fraction ) were added together in the ball mill cylinder, the ball mill balls were wear-resistant alumina balls, and the high-energy ball milled for 72 hours to obtain the mixture;
[0048] (3) Dry the mixture after ball milling in step (2) in a vacuum oven at a temperature of 130° C. for 0.5 h; pass through a 180-mesh sieve after drying;
[0049] (4) Put the composite raw material powder sieved in step (3) into a graphite mold, and p...
PUM
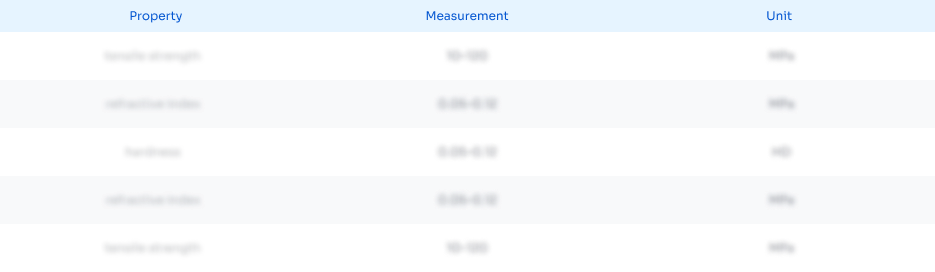
Abstract
Description
Claims
Application Information

- Generate Ideas
- Intellectual Property
- Life Sciences
- Materials
- Tech Scout
- Unparalleled Data Quality
- Higher Quality Content
- 60% Fewer Hallucinations
Browse by: Latest US Patents, China's latest patents, Technical Efficacy Thesaurus, Application Domain, Technology Topic, Popular Technical Reports.
© 2025 PatSnap. All rights reserved.Legal|Privacy policy|Modern Slavery Act Transparency Statement|Sitemap|About US| Contact US: help@patsnap.com