High speed bearing friction torque measuring system
A technology of friction torque and high-speed bearings, which is applied in mechanical bearing testing, measuring devices, torque measurement, etc., can solve the problems of inaccurate measurement of bearing friction torque and high axial load, etc., to reduce contact, reduce difficulty, The effect of improving loading capacity
- Summary
- Abstract
- Description
- Claims
- Application Information
AI Technical Summary
Problems solved by technology
Method used
Image
Examples
specific Embodiment approach 1
[0018] Specific implementation mode one: refer to figure 1 Describe this embodiment in detail, the high-speed bearing friction torque measurement system described in this embodiment, the system includes a main shaft support device 1, a main shaft 2, a sleeve 4, an axial load application device 5, an axial load measurement device 6 and a tension sensor 7,
[0019] The main shaft supporting device 1 is used to support the main shaft 2, and the two tested bearings 3 are respectively the No. 1 tested bearing 3-1 and the No. 2 tested bearing 3-2,
[0020] The No. 1 tested bearing 3-1, the No. 2 tested bearing 3-2, the axial load applying device 5 and the axial load measuring device 6 are all set on the main shaft 2, and there is a limit step on the main shaft 2 for limiting The axial position of No. 1 tested bearing 3-1,
[0021] The axial load measuring device 6 is arranged between the No. 1 tested bearing 3-1 and the No. 2 tested bearing 3-2, and is used to measure the axial lo...
specific Embodiment approach 2
[0030] Specific implementation mode two: refer to figure 2 Describe this embodiment in detail. This embodiment is a further description of the high-speed bearing friction torque measurement system described in Embodiment 1. In this embodiment, the system also includes a radial load application device,
[0031] The radial load applying device is connected to the bottom end of the outer wall of the sleeve 4 through a wire rope, and is used for applying radial load to the two tested bearings 3 .
specific Embodiment approach 3
[0032] Embodiment 3: This embodiment further explains the high-speed bearing friction torque measurement system described in Embodiment 2. In this embodiment, the radial load applying device is realized by using weights.
PUM
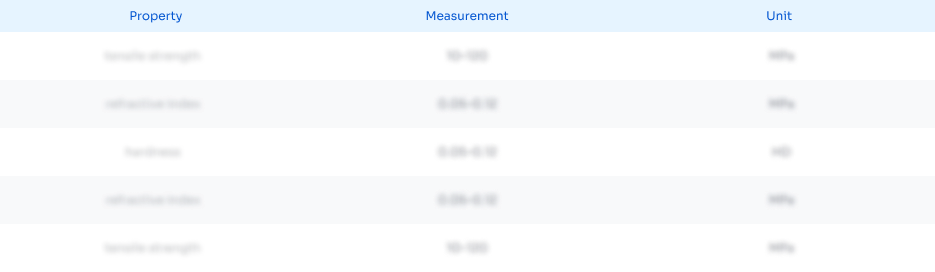
Abstract
Description
Claims
Application Information

- R&D
- Intellectual Property
- Life Sciences
- Materials
- Tech Scout
- Unparalleled Data Quality
- Higher Quality Content
- 60% Fewer Hallucinations
Browse by: Latest US Patents, China's latest patents, Technical Efficacy Thesaurus, Application Domain, Technology Topic, Popular Technical Reports.
© 2025 PatSnap. All rights reserved.Legal|Privacy policy|Modern Slavery Act Transparency Statement|Sitemap|About US| Contact US: help@patsnap.com