A method for producing sulfur-containing gear steel for wind power gears
A technology of sulfur gear steel and gears, which is applied in the field of producing sulfur-containing gear steel for wind power gears, and can solve the difficulty in controlling the production process of sulfur-containing gear steel, the unmention of beneficial effects such as shape control, and the instability of component content and uniformity and other problems, to achieve good cutting performance, reduce segregation of alloying elements, and excellent band structure
- Summary
- Abstract
- Description
- Claims
- Application Information
AI Technical Summary
Problems solved by technology
Method used
Image
Examples
Embodiment 1
[0051] The specification of the hot-rolled bar of sulfur-containing gear steel for wind power gears in this embodiment is φ50mm, and its production method includes: converter smelting, LF+RH refining, continuous casting, high-temperature diffusion, blanking, heating and rolling process flow;
[0052] The combined blowing converter adopts the bottom blowing large circular seam process. The carbon and oxygen product at the end of blowing is 0.0025%, and the carbon content at the end is 0.10wt%. Complete the sliding plate fully closed) Remaining steel operation reduces the amount of slag in the ladle, and adds a high-basicity aluminum-containing modifier with a binary basicity of 7.5 to modify the ladle slag, reducing the FeO content in the ladle slag to 1.2wt %;
[0053] LF adopts composite deoxidation process, and the final refining slag is operated with high alkalinity and low calcium-aluminum ratio. The binary basicity of the final slag is controlled at 4.3, and the calcium-a...
Embodiment 2
[0065] The specification of the hot-rolled bar of sulfur-containing gear steel for wind power gears in this embodiment is φ60mm, and its production method includes converter smelting, LF+RH refining, continuous casting, high-temperature diffusion, blanking, heating and rolling process flow;
[0066] The combined blowing converter adopts the bottom blowing large circular seam process to blow the end carbon and oxygen product to 0.0024%, and the end carbon content is 0.12wt%. The quality agent is used to modify the ladle slag, so that the FeO content in the ladle slag is reduced to 1.3wt%;
[0067] LF adopts the composite deoxidation process, and the final refining slag is operated with high alkalinity and low calcium-aluminum ratio. The binary alkalinity of the final slag is controlled at 4.5, and the calcium-aluminum ratio is controlled at 1.6;
[0068] RH high vacuum and large circulation operation (when the ultimate vacuum degree is ≤20Pa), feed the sulfur wire at an interva...
Embodiment 3
[0079] The specification of the hot-rolled bar of sulfur-containing gear steel for wind power gears in this embodiment is φ65mm, and the production method includes converter smelting, LF+RH refining, continuous casting, high-temperature diffusion, blanking, heating and rolling process flow;
[0080] The combined blowing converter adopts the bottom blowing large circular seam process to blow the end carbon and oxygen product to 0.0026%, and the end carbon content is 0.11wt%. The (FeO) content in the slag after quality is reduced to 1.4wt%;
[0081] LF adopts composite deoxidation process, and the final refining slag is operated with high alkalinity and low calcium-aluminum ratio. The binary basicity of the final slag is controlled at 4.6, and the calcium-aluminum ratio is controlled at 1.8;
[0082] RH high vacuum and large circulation operation (when the ultimate vacuum degree is ≤20Pa), feed the sulfur wire at intervals of 12 minutes after calcium treatment, and then soft blo...
PUM
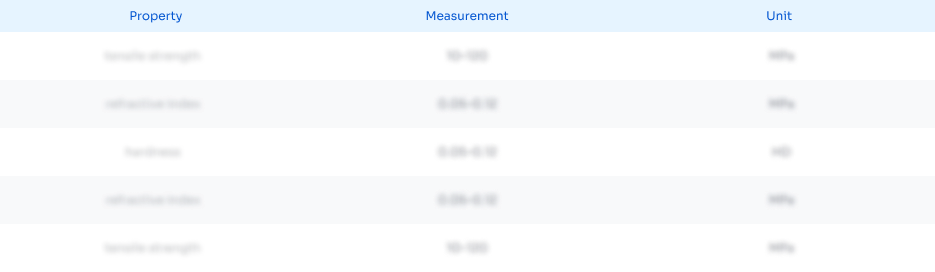
Abstract
Description
Claims
Application Information

- R&D
- Intellectual Property
- Life Sciences
- Materials
- Tech Scout
- Unparalleled Data Quality
- Higher Quality Content
- 60% Fewer Hallucinations
Browse by: Latest US Patents, China's latest patents, Technical Efficacy Thesaurus, Application Domain, Technology Topic, Popular Technical Reports.
© 2025 PatSnap. All rights reserved.Legal|Privacy policy|Modern Slavery Act Transparency Statement|Sitemap|About US| Contact US: help@patsnap.com