Copper plating method for ceramic substrate
A ceramic substrate and copper plating technology, applied in the electrolytic process, electrolytic components, etc., can solve the problems of poor copper plating thickness uniformity, uneven distribution of power lines, affecting the service life of packaging and finished products, etc., to improve cleanliness, good copper The effect of coating adhesion
- Summary
- Abstract
- Description
- Claims
- Application Information
AI Technical Summary
Problems solved by technology
Method used
Image
Examples
Embodiment 1
[0092] The copper plating method of a kind of ceramic substrate that present embodiment provides, comprises the following steps:
[0093] (1) Mount the ceramic substrate 3 on the mounting hole 11 of the first hanger 1 .
[0094] (2) Carry out surface pretreatment to the first hanger 1 and the ceramic substrate 3; Wherein, the surface pretreatment step is carried out sequentially according to the following steps:
[0095] Degreasing: Soak in surfactant for 90s;
[0096] Pickling: Soak in 4% H by volume fraction 2 60s in SO;
[0097] Double washing: Soak in two water-filled washing tanks for 60 seconds each;
[0098] Hot water washing: Soak in hot water at 60°C for 60s.
[0099] (3) Copper electroplating for the first time: the first hanger 1 is suspended on the cathode rod of the copper plating tank 4, and the phosphor copper ball is selected as the anode 5; the ceramic substrate 3 is completely immersed in the electroplating solution 6 for the first electroplating of coppe...
Embodiment 2
[0110] The copper plating method of a kind of ceramic substrate that present embodiment provides, and the difference of embodiment 1 is:
[0111] In step (7) second electroplating copper, the ratio of the thickness of the first copper layer 31 and the thickness of the second copper layer 32 is 1.8:1, the thickness of the first copper layer 31 and the thickness of the second copper layer 32 form The copper plating thickness is 70 μm.
Embodiment 3
[0113] The copper plating method of a kind of ceramic substrate that present embodiment provides, and the difference of embodiment 1 is:
[0114] In step (7) second electroplating copper, the ratio of the thickness of the first copper layer 31 and the thickness of the second copper layer 32 is 2.2:1, the thickness of the first copper layer 31 and the thickness of the second copper layer 32 form The copper plating thickness is 80 μm.
PUM
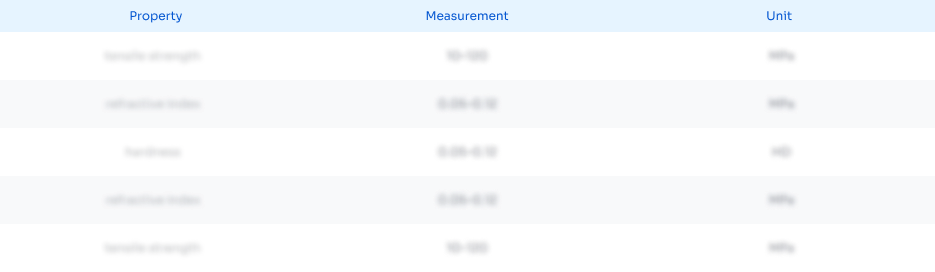
Abstract
Description
Claims
Application Information

- Generate Ideas
- Intellectual Property
- Life Sciences
- Materials
- Tech Scout
- Unparalleled Data Quality
- Higher Quality Content
- 60% Fewer Hallucinations
Browse by: Latest US Patents, China's latest patents, Technical Efficacy Thesaurus, Application Domain, Technology Topic, Popular Technical Reports.
© 2025 PatSnap. All rights reserved.Legal|Privacy policy|Modern Slavery Act Transparency Statement|Sitemap|About US| Contact US: help@patsnap.com