Fluorine-modified anionic polyurethane emulsion and preparation method thereof
A polyurethane emulsion and anion technology, applied in the direction of repelling fibers to liquids, textiles and papermaking, fiber processing, etc., can solve the problems of unstable emulsion, poor water and oil repellency, etc., and achieve less raw material consumption and cost. Low, simple process effect
- Summary
- Abstract
- Description
- Claims
- Application Information
AI Technical Summary
Problems solved by technology
Method used
Image
Examples
Embodiment 1
[0031] A fluorine-modified anionic polyurethane emulsion, in parts by weight, its raw material components include: 4,4`-diphenylmethane diisocyanate: 75 parts, polybutylene adipate: 110 parts, 2, 2-dimethylolpropionic acid: 16 parts, perfluoroalkylethanol: 18 parts, trimethylolpropane: 6.3 parts, triethylamine: 15 parts, butanone: 200 parts, deionized water: 900 parts.
[0032] The present invention also provides a preparation method for the above-mentioned fluorine-modified anionic polyurethane emulsion, comprising the steps of:
[0033] 1. Prepolymerization: Add 4,4`-diphenylmethane diisocyanate, polybutylene adipate, fluoroalcohol and cross-linking agent in 150 parts by weight of butanone solution according to the above ratio. Under the conditions, start timing when the temperature rises to 63°C, control the temperature between 63°C and 70°C, and react for 1.5 hours to form a prepolymerization solution.
[0034] 2. Chain extension: Dissolve 2,2-dimethylolpropionic acid wit...
Embodiment 2
[0045] A fluorine-modified anionic polyurethane emulsion, the emulsion raw materials and their proportioning are the same as in Example 1. The only difference is that the perfluoroalkyl alcohol in Example 2 is 10 parts by weight.
[0046] The present invention also provides a preparation method for the above-mentioned fluorine-modified anionic polyurethane emulsion, comprising the steps of:
[0047] 1. Prepolymerization: Add 4,4`-diphenylmethane diisocyanate, polybutylene adipate, fluoroalcohol, and crosslinking agent to 150 parts by weight of methyl ethyl ketone solution, under the condition of nitrogen protection, Start timing when the temperature rises to 72°C, control the temperature between 75°C and 80°C, and react for 2.5 hours to form a prepolymer solution.
[0048] 2. Chain extension: Dissolve 2,2-dimethylolpropionic acid with 50 parts by weight of methyl ethyl ketone, slowly add it to the prepolymerization solution, start timing when the temperature rises to 80°C, an...
Embodiment 3
[0053]A fluorine-modified anionic polyurethane emulsion, the emulsion raw materials and their proportioning are the same as in Example 1. The only difference is that the perfluoroalkyl alcohol in Example 2 is 14 parts by weight.
[0054] The present invention also provides a preparation method for the above-mentioned fluorine-modified anionic polyurethane emulsion, comprising the steps of:
[0055] 1. Prepolymerization: Add 4,4`-diphenylmethane diisocyanate, polybutylene adipate, fluoroalcohol, and crosslinking agent to 150 parts by weight of methyl ethyl ketone solution, under the condition of nitrogen protection, Start timing when the temperature rises to 63°C, control the temperature between 63°C and 75°C, and react for 2 hours to form a prepolymer solution.
[0056] 2. Chain extension: Dissolve 2,2-dimethylolpropionic acid with 50 parts by weight of methyl ethyl ketone, slowly add it to the prepolymerization solution, start timing when the temperature rises to 78°C, and c...
PUM
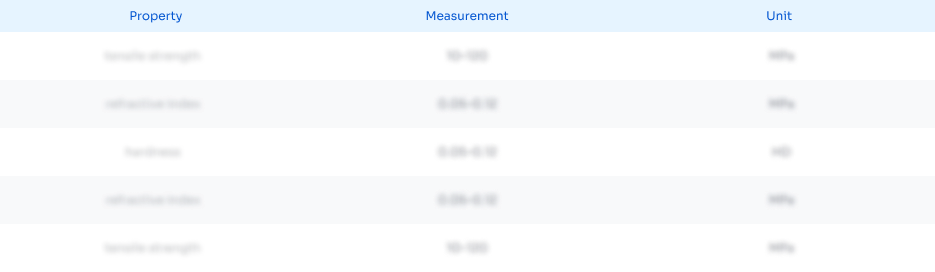
Abstract
Description
Claims
Application Information

- R&D Engineer
- R&D Manager
- IP Professional
- Industry Leading Data Capabilities
- Powerful AI technology
- Patent DNA Extraction
Browse by: Latest US Patents, China's latest patents, Technical Efficacy Thesaurus, Application Domain, Technology Topic, Popular Technical Reports.
© 2024 PatSnap. All rights reserved.Legal|Privacy policy|Modern Slavery Act Transparency Statement|Sitemap|About US| Contact US: help@patsnap.com