Heavy duty vehicle bearing beam machining process
A processing technology and load-bearing beam technology, applied in vehicle parts, transportation and packaging, etc., can solve the problems of long mold change time, poor flexible processing ability, high mold cost, etc., and achieve high flexibility, high hole position accuracy, and manufacturing low cost effect
- Summary
- Abstract
- Description
- Claims
- Application Information
AI Technical Summary
Problems solved by technology
Method used
Examples
Embodiment Construction
[0019] In order to enable those skilled in the art to better understand the technical solutions of the present invention, the present invention will be further described in detail below in conjunction with specific embodiments.
[0020] The present invention comprises the following steps:
[0021] A. Roll forming.
[0022] Considering that the structure of the heavy-duty vehicle frame load-bearing beam is basically a U-shaped beam structure with a constant section, the forming of a U-shaped beam with a constant section is the advantage of roll forming. In addition, due to the large variety of frame load-bearing beams, small batches, and a variety of load-bearing beams with different outer widths and material thickness specifications are produced every day, this requires the roll forming line to have 1 coil rewinding function 2 convenient process parameter conversion 3 cutting tools Cannot be replaced frequently.
[0023] The main components of the roll forming line are: feed...
PUM
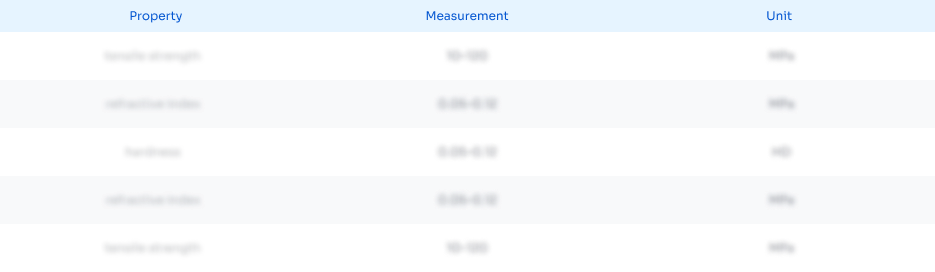
Abstract
Description
Claims
Application Information

- R&D
- Intellectual Property
- Life Sciences
- Materials
- Tech Scout
- Unparalleled Data Quality
- Higher Quality Content
- 60% Fewer Hallucinations
Browse by: Latest US Patents, China's latest patents, Technical Efficacy Thesaurus, Application Domain, Technology Topic, Popular Technical Reports.
© 2025 PatSnap. All rights reserved.Legal|Privacy policy|Modern Slavery Act Transparency Statement|Sitemap|About US| Contact US: help@patsnap.com