Low-odor rolling oil for steel cold rolling and use method of rolling oil
A technology for rolling oil and peculiar smell, applied in the field of rolling oil, can solve the problems affecting the lubricity of rolling oil, low peculiar smell, and no special explanation, and achieve the effect of reducing atomization effect and reducing peculiar smell
- Summary
- Abstract
- Description
- Claims
- Application Information
AI Technical Summary
Problems solved by technology
Method used
Examples
Embodiment 1
[0037] Natural oils: palm oil 0;
[0038] Synthetic Lubricant: Trimethylolpropane Hexadecanoate 90%;
[0039] Surfactant: nonylphenol polyoxyethylene ether 1.5%, tallow amine polyoxyethylene ether 1.5%;
[0040] Extreme pressure antiwear agent: neopentyl glycol oleic acid synthetic ester 2.5%, phosphoric acid ester 3%
[0041] Antioxidant additive: 2,6-diisobutyl p-cresol 1.5%
[0042] Apply the emulsion prepared by the above-mentioned rolling oil to the scene, control the temperature of the emulsion at 55°C, the concentration is 1.5% in the #1-#4 stand of the cold rolling mill, and the iron powder concentration in the emulsion is controlled at 120ppm; The #5 rack of the continuous rolling mill uses a concentration of 0.7%, and the iron powder concentration of the emulsion is controlled at 65ppm.
[0043] The emulsion odor concentration measured in the equipment exhaust chimney of the cold rolling mill is 41.
Embodiment 2
[0045] Natural oils: palm oil 18%;
[0046] Synthetic Lubricant: Trimethylolpropane Hexadecanoate 75%;
[0047] Surfactant: 1% nonylphenol polyoxyethylene ether, 1% fatty alcohol polyoxyethylene ether with 16 carbon atoms;
[0048] Extreme pressure antiwear agent: Phosphate 4%
[0049] Antioxidant additive: 2,6-diisobutyl p-cresol 1%
[0050]Apply the emulsion prepared by the above-mentioned rolling oil to the field, control the temperature of the emulsion at 50°C, the concentration is 2.5% in the #1-#4 stands of the cold rolling mill, and the concentration of iron powder in the emulsion is controlled at 230ppm; The #5 rack of the continuous rolling mill uses a concentration of 0.8%, and the iron powder concentration of the emulsion is controlled at 95ppm.
[0051] The emulsion odor concentration measured in the equipment exhaust chimney of the cold rolling mill is 70%.
Embodiment 3
[0053] Natural oils: palm oil 25%;
[0054] Synthetic lubricating ester: trimethylolpropane hexadecanoate 67%;
[0055] Surfactant: nonylphenol polyoxyethylene ether 0.5%, octylphenol polyoxyethylene ether 0.5%, tallow amine polyoxyethylene ether 1%;
[0056] Extreme pressure antiwear agent: neopentyl glycol oleic acid synthetic ester 4.5% sulfurized
[0057] Antioxidant additive: 2,6-diisobutyl p-cresol 1.5%
[0058] Apply the emulsion prepared by the above-mentioned rolling oil to the field, control the temperature of the emulsion at 52°C, the concentration is 1.7% in the #1-#4 stands of the cold rolling mill, and the concentration of iron powder in the emulsion is controlled at 200ppm; The #5 rack of the continuous rolling mill uses a concentration of 0.8%, and the iron powder concentration of the emulsion is controlled at 87ppm.
[0059] The emulsion odor concentration measured in the equipment exhaust chimney of the cold rolling mill is 173.
PUM
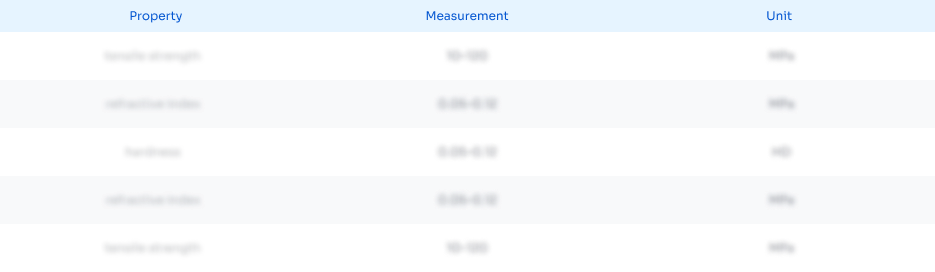
Abstract
Description
Claims
Application Information

- Generate Ideas
- Intellectual Property
- Life Sciences
- Materials
- Tech Scout
- Unparalleled Data Quality
- Higher Quality Content
- 60% Fewer Hallucinations
Browse by: Latest US Patents, China's latest patents, Technical Efficacy Thesaurus, Application Domain, Technology Topic, Popular Technical Reports.
© 2025 PatSnap. All rights reserved.Legal|Privacy policy|Modern Slavery Act Transparency Statement|Sitemap|About US| Contact US: help@patsnap.com