Sensorless brushless DC motor commutation position correction system and method
A brushed DC motor and sensor technology, applied in the control system, electronic commutation motor control, electrical components, etc., can solve the problems of poor motor control and operation performance, inaccurate commutation position detection, commutation position deviation, etc. Achieve fast and accurate correction, improve control and operation performance, and achieve the effect of less detection
- Summary
- Abstract
- Description
- Claims
- Application Information
AI Technical Summary
Problems solved by technology
Method used
Image
Examples
Embodiment Construction
[0048] In order to make the technical means, creative features, goals and effects achieved by the present invention easy to understand, the present invention will be further described below in conjunction with specific embodiments.
[0049] attached figure 1 It is the sensorless brushless DC motor commutation position correction system of the present invention, including a DC power supply 1, a three-phase full-bridge inverter 2, a brushless DC motor 3, a terminal voltage step-down and filter circuit 4, and a back EMF zero-crossing point Detection circuit 5, DC bus and b-phase terminal voltage detection circuit 6, digital signal processor 7, PWM signal drive circuit 8;
[0050] The three-phase full-bridge inverter 2 inverts the DC power provided by the DC power supply 1 into AC power to supply power to the three-phase windings of the brushless DC motor 3, and the terminal voltage of the three-phase windings of the brushless DC motor 3 passes through the terminal voltage step-do...
PUM
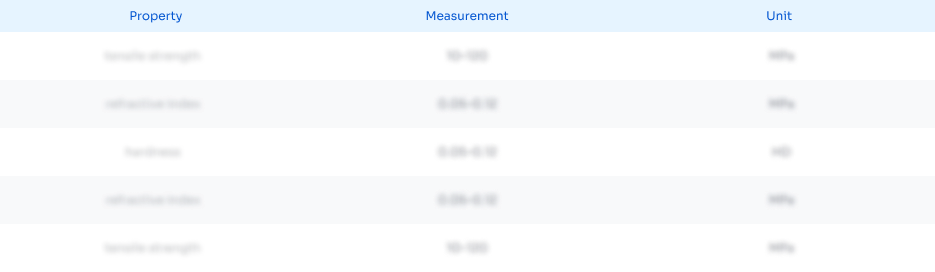
Abstract
Description
Claims
Application Information

- R&D
- Intellectual Property
- Life Sciences
- Materials
- Tech Scout
- Unparalleled Data Quality
- Higher Quality Content
- 60% Fewer Hallucinations
Browse by: Latest US Patents, China's latest patents, Technical Efficacy Thesaurus, Application Domain, Technology Topic, Popular Technical Reports.
© 2025 PatSnap. All rights reserved.Legal|Privacy policy|Modern Slavery Act Transparency Statement|Sitemap|About US| Contact US: help@patsnap.com