Multi-port millimeter wave bent rectangular waveguide array body integrated whole manufacturing method
A rectangular waveguide and manufacturing method technology, which is applied in the field of integrated manufacturing of multi-port millimeter-wave curved rectangular waveguide arrays, can solve the problem of affecting transmission, unable to meet the requirements of inner cavity dimensional accuracy, inner cavity roughness and sealing, and unable to achieve sealing and other issues to achieve the effect of meeting the requirements of assembly accuracy and waveguide transmission performance
- Summary
- Abstract
- Description
- Claims
- Application Information
AI Technical Summary
Problems solved by technology
Method used
Image
Examples
Embodiment Construction
[0029] The present invention will be described in further detail below in conjunction with the accompanying drawings, but the embodiments of the present invention are not limited thereto.
[0030] Such as figure 1 As shown, the integrated manufacturing method of the multi-port millimeter wave curved rectangular waveguide array body includes:
[0031] (1) Manufacturing the shape mold of the multi-port millimeter-wave rectangular curved waveguide array body and the water-soluble core forming mold of the waveguide inner cavity;
[0032] For the three-dimensional part of the waveguide array body, Pro / E is used to divide the mold, determine the total shrinkage rate, and create the waveguide cavity; the cavity is divided into the following parts: (1) The waveguide cavity of the main mold forming the shape structure is divided (2) The core model cavity forming the waveguide cavity structure is divided into two parts; use the Extract function in Mold Comp to generate the model entity...
PUM
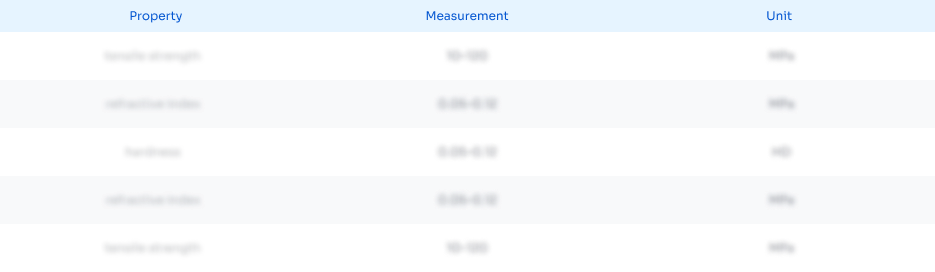
Abstract
Description
Claims
Application Information

- R&D
- Intellectual Property
- Life Sciences
- Materials
- Tech Scout
- Unparalleled Data Quality
- Higher Quality Content
- 60% Fewer Hallucinations
Browse by: Latest US Patents, China's latest patents, Technical Efficacy Thesaurus, Application Domain, Technology Topic, Popular Technical Reports.
© 2025 PatSnap. All rights reserved.Legal|Privacy policy|Modern Slavery Act Transparency Statement|Sitemap|About US| Contact US: help@patsnap.com