A method for preparing low-magnesium calcium sulfate dihydrate by-product from rare earth sulfate solution
A low-magnesium calcium sulfate dihydrate, rare earth sulfate technology, applied in the direction of calcium/strontium/barium sulfate, process efficiency improvement, etc., can solve the problems of high oxalic acid price, oxalic acid toxicity, high cost, etc., and achieve high rare earth yield, Significant economic benefits and low production costs
- Summary
- Abstract
- Description
- Claims
- Application Information
AI Technical Summary
Problems solved by technology
Method used
Image
Examples
Embodiment 1
[0019] Example 1, take 1 L of a rare earth sulfate solution with a concentration of 30 g / L and an acidity of 0.4 mol / L, and prepare a calcium hydroxide slurry with a mass ratio of calcium hydroxide to aqueous solution of 1:20. The prepared calcium hydroxide slurry was evenly added dropwise to the rare earth sulfate solution at a flow rate of 4.5ml / min with a peristaltic pump under stirring for neutralization reaction. The neutralization reaction temperature was controlled at 40°C, and the reaction time was 60min. : 1.5~2.0, after the reaction, stir and age for 120min, filter the precipitate, the filtrate is clear, and the total rare earth yield of sulfuric acid rare earth solution reaches 99.96%. The prepared CaSO 4 2H 2 O, washed twice with 0.1mol / L dilute sulfuric acid solution, then rinsed once with tap water, the filtrate basically has no rare earth content (trace 0.03g / l), and the rare earth is recovered from the filtrate. Dry the filter cake at 40°C to obtain CaSO 4 2...
Embodiment 2
[0020] Example 2, take 1 L of rare earth sulfate solution with a concentration of 14.5 g / L and an acidity of 0.2 mol / L, and prepare a calcium hydroxide slurry with a mass ratio of calcium hydroxide to aqueous solution of 1:10. The prepared calcium hydroxide slurry was evenly added dropwise into the rare earth sulfate solution at a flow rate of 9ml / min with a peristaltic pump under stirring to carry out neutralization reaction. The neutralization reaction temperature was controlled at 25°C, and the reaction time was 30min. : 1.5~2.0, after the reaction, stir and age for 60min, filter the precipitate, the filtrate is clear, and the total rare earth yield of sulfuric acid rare earth solution reaches 99.95%. The prepared CaSO 4 2H 2 O, wash twice with 0.5mol / L dilute sulfuric acid solution, then rinse once with tap water, the filtrate has almost no rare earth content (trace 0.03g / l), and dry the filter cake at 40°C to obtain CaSO 4 2H 2 O samples. XRD diffraction as image 3 ...
Embodiment 3
[0021] Example 3, take 1 L of a rare earth sulfate solution with a concentration of 24.8 g / L and an acidity of 0.34 mol / L, and prepare a calcium hydroxide slurry with a mass ratio of calcium hydroxide to aqueous solution of 1:10. The prepared calcium hydroxide slurry was uniformly added dropwise into the rare earth sulfate solution at a flow rate of 4.9ml / min with a peristaltic pump under stirring to carry out neutralization reaction. The neutralization reaction temperature was controlled at 30°C, and the neutralization reaction time was 55min. PH: 1.5-2.0, after the reaction, stir and age for 90 minutes, filter the precipitate, the filtrate is clear, and the total rare earth yield of sulfuric acid rare earth solution reaches 99.98%. The prepared CaSO 4 2H 2 O, wash twice with 0.5mol / L dilute sulfuric acid solution, then rinse once with tap water, the filtrate has almost no rare earth content (trace 0.03g / l), and dry the filter cake at 30°C to obtain CaSO 4 2H 2 O sample, X...
PUM
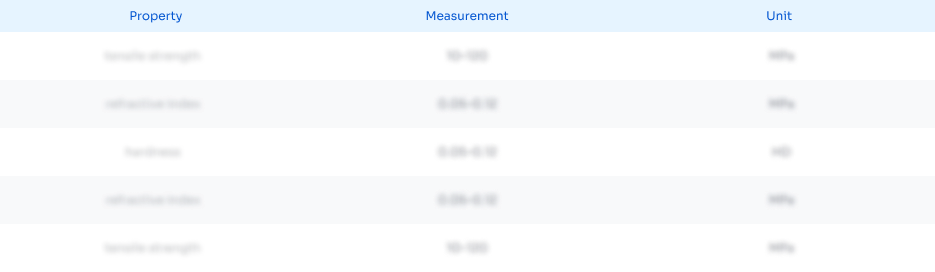
Abstract
Description
Claims
Application Information

- R&D
- Intellectual Property
- Life Sciences
- Materials
- Tech Scout
- Unparalleled Data Quality
- Higher Quality Content
- 60% Fewer Hallucinations
Browse by: Latest US Patents, China's latest patents, Technical Efficacy Thesaurus, Application Domain, Technology Topic, Popular Technical Reports.
© 2025 PatSnap. All rights reserved.Legal|Privacy policy|Modern Slavery Act Transparency Statement|Sitemap|About US| Contact US: help@patsnap.com