Method of pulsed deposition of nano tin dots on medium and high voltage anodic aluminium foils for aluminium electrolytic capacitors
A pulse deposition, anode aluminum foil technology, applied in electrolytic capacitors, capacitors, circuits, etc., can solve the problems of reducing the mechanical properties of aluminum foil and restricting the uniformity and size consistency of aluminum foil, tin, zinc crystal nucleus distribution and so on
- Summary
- Abstract
- Description
- Claims
- Application Information
AI Technical Summary
Problems solved by technology
Method used
Image
Examples
Embodiment 1
[0016] Put Mn, Fe, Co, Ni, Cu, Zn, Cd, Ga, Ge, In, Sn, Pb elements whose surface is not rich in electrode potential higher than aluminum, and high-purity medium-high-voltage aluminum foil with a purity of 99.99% at a temperature of 40°C , the solution composition is 0.5mol / L sodium hydroxide + 0.1mol / L potassium sodium tartrate for 30 seconds to remove the natural oxide film on the surface. Place the above-mentioned aluminum foil for pulse deposition, and the solution composition is: 0.01mol / L sodium stannate trihydrate + 0.5mol / L sodium hydroxide + 0.1mol / L potassium sodium tartrate; graphite is used as the anode, and the above-mentioned pretreated The medium and high voltage aluminum foil is used as the cathode, and the aluminum foil is charged into the electrolyte solution, where the temperature of the electroplating solution is 30°C, and the current density of pulse deposition is 40mA / cm 2 , the pulse time is 1s, the interval between each pulse is 1s, and the total time is...
Embodiment 2
[0019] Put Mn, Fe, Co, Ni, Cu, Zn, Cd, Ga, Ge, In, Sn, Pb elements whose surface is not enriched with higher electrode potential than aluminum, and high-purity medium-high-voltage aluminum foil with a purity of 99.99% at a temperature of 60°C , the solution composition is 1.5 mol / L sodium hydroxide + 0.3 mol / L potassium sodium tartrate and pretreated for 60 seconds to remove the natural oxide film on the surface. Place the above-mentioned aluminum foil for pulse deposition, and the solution composition is: 0.01mol / L sodium stannate trihydrate + 0.5mol / L sodium hydroxide + 0.1mol / L potassium sodium tartrate; graphite is used as the anode, and the above-mentioned pretreated The medium and high voltage aluminum foil is used as the cathode, and the aluminum foil is charged into the electrolyte solution, where the temperature of the electroplating solution is 30°C, and the current density of pulse deposition is 40mA / cm 2 , the pulse time is 1s, the interval between each pulse is 1s...
Embodiment 3
[0022] Put Mn, Fe, Co, Ni, Cu, Zn, Cd, Ga, Ge, In, Sn, Pb elements whose surface is not rich in electrode potential higher than aluminum, and high-purity medium-high-voltage aluminum foil with a purity of 99.99% at a temperature of 40°C , the solution is composed of 3.5mol / L sodium hydroxide + 0.5mol / L potassium sodium tartrate and pretreated for 150 seconds to remove the natural oxide film on the surface. Place the above aluminum foil for pulse deposition, and the solution composition is: 0.01mol / L sodium stannate trihydrate + 0.5mol / L sodium hydroxide + 0.1mol / L potassium sodium tartrate; graphite is used as the anode, and the above pretreated The medium and high voltage aluminum foil is used as the cathode, and the aluminum foil is charged into the electrolyte solution, where the temperature of the electroplating solution is 30°C, and the current density of pulse deposition is 40mA / cm 2 , the pulse time is 1s, the interval between each pulse is 1s, and the total time is 20 ...
PUM
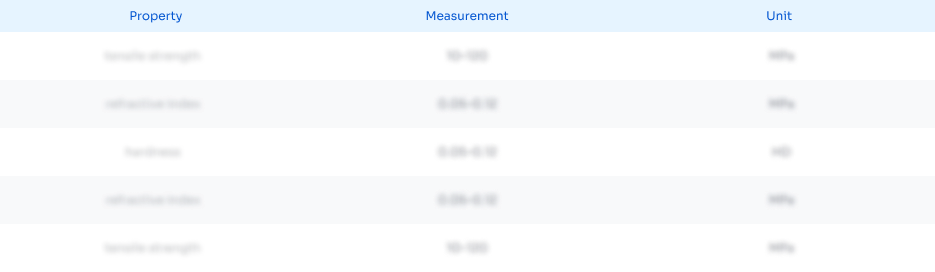
Abstract
Description
Claims
Application Information

- Generate Ideas
- Intellectual Property
- Life Sciences
- Materials
- Tech Scout
- Unparalleled Data Quality
- Higher Quality Content
- 60% Fewer Hallucinations
Browse by: Latest US Patents, China's latest patents, Technical Efficacy Thesaurus, Application Domain, Technology Topic, Popular Technical Reports.
© 2025 PatSnap. All rights reserved.Legal|Privacy policy|Modern Slavery Act Transparency Statement|Sitemap|About US| Contact US: help@patsnap.com