Thermoplastic elastomer material, and preparation method thereof
A thermoplastic elastomer and raw material technology, applied in the field of thermoplastic elastomer materials and their preparation, to achieve low compression set, low equipment requirements, and good tear resistance
- Summary
- Abstract
- Description
- Claims
- Application Information
AI Technical Summary
Problems solved by technology
Method used
Image
Examples
preparation example Construction
[0055] The preparation method of above-mentioned thermoplastic elastomer material, comprises the following steps:
[0056] S110, uniformly stirring the TPV, the lubricant, and the maleic anhydride-grafted polypropylene to obtain a first mixture.
[0057] In one embodiment, the stirring is carried out in a horizontal mixer, and the stirring rate is 20r / min-40r / min, preferably 30r / min-40r / min.
[0058] In one of the embodiments, stirring is carried out at room temperature (23° C.) for 5 min to 10 min, preferably 8 min to 10 min.
[0059] S120. Mix and stir the first mixture evenly with the mineral filler, UV absorber, modified polyethylene wax and antioxidant to obtain a premix.
[0060] In one embodiment, the stirring is carried out in a horizontal stirrer, and the stirring rate is 40r / min-60r / min, preferably 50r / min-60r / min.
[0061] In one of the embodiments, stirring is carried out at room temperature (23° C.) for 10 min to 15 min, preferably 20 r / min to 40 r / min.
[0062...
Embodiment 1
[0070] Put 90 parts of American santoprene's TPV101-55 into a horizontal mixer, add 3 parts of Exxon Mobil's maleic anhydride grafted polypropylene PO1020 and 5.5 parts of Dow Corning's lubricant MB50-001, at room temperature (23 ℃ ) and a rotation speed of 20 r / min for 5 min to obtain the first mixture.
[0071] Put the first mixture into a horizontal mixer, add 1 part of mineral filler SiO 2 , 0.5 parts of Clariant's polytetrafluoroethylene modified polyethylene wax 3920F, 0.15 parts of antioxidant (Basf's antioxidant 168 and antioxidant 1076 are compounded in a ratio of 2:1) and 0.1 part of UV absorbing Agent UV-P, stirred for 10 minutes at room temperature with a rotational speed of 40r / min to obtain a premix.
[0072] The premix was extruded in a twin-screw extruder with a rotation speed of 150 r / min and a length-to-diameter ratio of 24:1, and pelletized to obtain a thermoplastic elastomer material.
Embodiment 2
[0074] Put 85 parts of American santoprene's TPV101-55 into a horizontal mixer, add 8 parts of Exxon Mobil's maleic anhydride grafted polypropylene PO1020 and 2 parts of Dow Corning's lubricant MB50-001, at room temperature (23°C) Under the condition of 40r / min, the rotation speed was stirred for 10min to obtain the first mixture;
[0075] The first mixture is put into a horizontal mixer, adding 4.5 parts of mineral filler carbon black, 0.5 part of Clariant's polytetrafluoroethylene modified polyethylene wax 3920F, 0.15 parts of antioxidant (Basf's antioxidant 168 Mix with antioxidant 1076 at a ratio of 2:1) and 0.2 parts of ultraviolet absorber UV-770, and stir for 10 minutes at room temperature (23°C) at a speed of 60r / min to obtain a premix.
[0076] Put the premix into a twin-screw extruder with a rotating speed of 200r / min and a length-to-diameter ratio of 36:1 to extrude and pelletize to obtain a thermoplastic elastomer material.
PUM
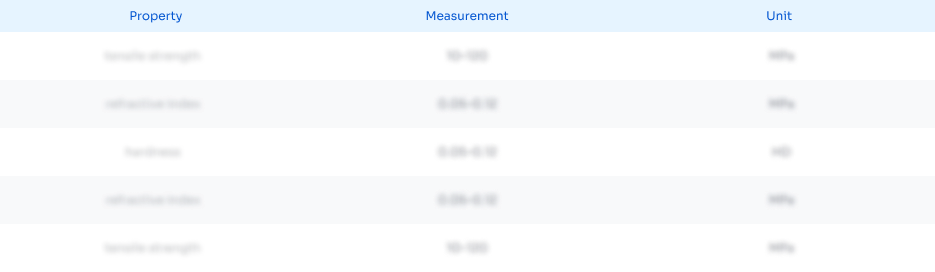
Abstract
Description
Claims
Application Information

- R&D
- Intellectual Property
- Life Sciences
- Materials
- Tech Scout
- Unparalleled Data Quality
- Higher Quality Content
- 60% Fewer Hallucinations
Browse by: Latest US Patents, China's latest patents, Technical Efficacy Thesaurus, Application Domain, Technology Topic, Popular Technical Reports.
© 2025 PatSnap. All rights reserved.Legal|Privacy policy|Modern Slavery Act Transparency Statement|Sitemap|About US| Contact US: help@patsnap.com