Method for manufacturing additives and method for refining molten steel using the same
An additive preparation and additive technology, which is applied in the field of additive preparation and molten iron refining, can solve the problems of sulfur increase and high content, and achieve the effects of improving dephosphorization rate and desulfurization rate, improving refining rate, and reducing sludge landfill
- Summary
- Abstract
- Description
- Claims
- Application Information
AI Technical Summary
Problems solved by technology
Method used
Image
Examples
preparation example Construction
[0037] The invention relates to an additive preparation method for reusing sludge generated in a steelmaking process. More specifically, the present invention provides a method for preparing an additive. The additive is prepared by reusing steelmaking sludge. Adding the additive during refining can prevent the increase of sulfur (S) in molten iron, and is harmful to the environment. friendly.
[0038] figure 1 is a flowchart illustrating an additive preparation method according to an embodiment of the present invention. figure 2 is a block diagram showing an additive preparation apparatus according to an embodiment of the present invention. image 3 is a block diagram showing an additive preparation apparatus according to a first modification of the embodiment. Figure 4 is a block diagram showing an additive preparation apparatus according to a second modification of the embodiment.
[0039] The additive preparation method according to the embodiment of the present inven...
PUM
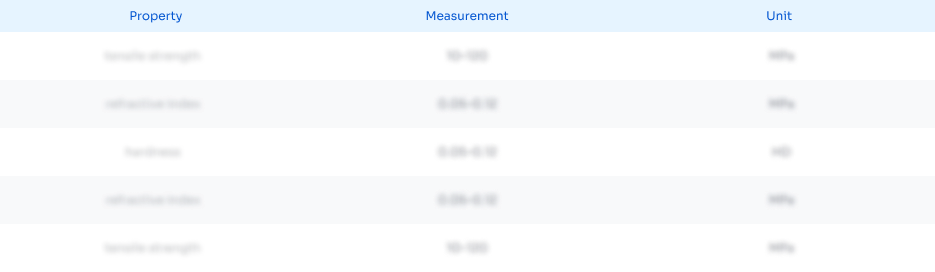
Abstract
Description
Claims
Application Information

- Generate Ideas
- Intellectual Property
- Life Sciences
- Materials
- Tech Scout
- Unparalleled Data Quality
- Higher Quality Content
- 60% Fewer Hallucinations
Browse by: Latest US Patents, China's latest patents, Technical Efficacy Thesaurus, Application Domain, Technology Topic, Popular Technical Reports.
© 2025 PatSnap. All rights reserved.Legal|Privacy policy|Modern Slavery Act Transparency Statement|Sitemap|About US| Contact US: help@patsnap.com