Measuring Method of Aperture Size of Parts Based on Machine Vision Technology
A technology of machine vision and measurement methods, applied in measurement devices, instruments, image analysis, etc., can solve the problems of cumbersome process, difficult calibration of parts hole surface, low accuracy, etc., to simplify the measurement process, improve measurement accuracy, and correct image distortion. Effect
- Summary
- Abstract
- Description
- Claims
- Application Information
AI Technical Summary
Problems solved by technology
Method used
Image
Examples
Embodiment Construction
[0038] The detailed content and specific embodiments of the present invention will be further described below in conjunction with the accompanying drawings.
[0039] See Figure 1 to Figure 6 As shown, the method for measuring part aperture size based on machine vision technology of the present invention uses the conditions for setting the formation of the world coordinate system I to establish the transformation relationship equation between the world coordinate system I and the camera coordinate system, thereby establishing the aperture measurement model; this method It is first proposed to place three small circular tubes of the same size in the part hole and collect the image of the part hole end surface, and obtain the curve equation of the inner and outer edge of the small circular tube end surface by curve fitting on the theoretical image plane. Establish new world coordinate systems II and III based on the adjacent small circular tubes, obtain the world coordinates of the ...
PUM
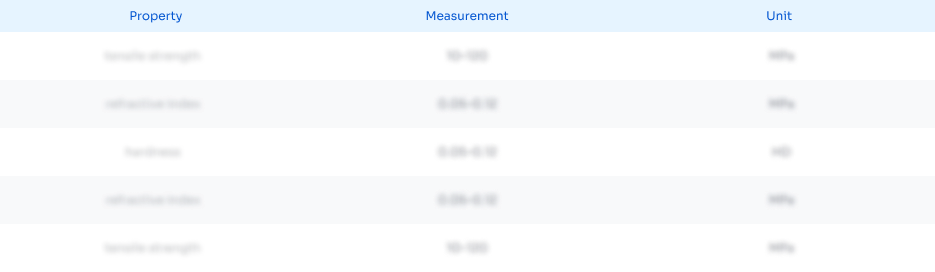
Abstract
Description
Claims
Application Information

- R&D
- Intellectual Property
- Life Sciences
- Materials
- Tech Scout
- Unparalleled Data Quality
- Higher Quality Content
- 60% Fewer Hallucinations
Browse by: Latest US Patents, China's latest patents, Technical Efficacy Thesaurus, Application Domain, Technology Topic, Popular Technical Reports.
© 2025 PatSnap. All rights reserved.Legal|Privacy policy|Modern Slavery Act Transparency Statement|Sitemap|About US| Contact US: help@patsnap.com