120-180 degree heat dissipation and non-side-leakage liquid metal heat interface material
A technology of thermal interface materials and liquid metals, applied in the field of indium alloys, can solve problems such as no solutions, and achieve the effects of low production costs, large market value, and simple processing and smelting methods
- Summary
- Abstract
- Description
- Claims
- Application Information
AI Technical Summary
Problems solved by technology
Method used
Image
Examples
Embodiment 1
[0017] A liquid metal thermal interface material with 120-180 degree heat dissipation and no side leakage. In terms of weight percentage, the composition of the alloy is: Al: 0.5wt.%, Co: 0.2wt.%, Ga: 1.0wt.%, V: 0.2wt.%, Zn: 28.0wt.%, Ge: 1.5wt. %, Sb: 3.0wt.%, the balance is indium.
[0018] The preparation method of the above-mentioned heat dissipation material includes the following processing steps: (a) After the alloy is configured according to the required components, it is put into an induction furnace for melting, and is protected by a graphite crucible and argon; heat preservation at 300-400 degrees for 10 minutes After the alloy melt is fully stirred evenly by electromagnetic stirring, it is introduced into the graphite mold for casting; (b) The ingot is cold-rolled, and the reduction of each rolling pass is 10-20% until the required rolling is achieved. Thickness (0.1-0.5mm).
[0019] The melting point of the matrix phase of the material is 190 degrees, while the...
Embodiment 2
[0021] A liquid metal thermal interface material with 120-180 degree heat dissipation and no side leakage. In terms of weight percentage, the composition of the alloy is: Al: 1.0wt.%, Co: 0.4wt.%, Ga: 1.5wt.%, V: 0.4wt.%, Zn: 34.0wt.%, Ge: 2.0wt. %, Sb: 4.0wt.%, the balance is indium.
[0022] The preparation method of the above-mentioned heat dissipation material includes the following processing steps: (a) After the alloy is configured according to the required components, it is put into an induction furnace for melting, and is protected by a graphite crucible and argon; heat preservation at 300-400 degrees for 10 minutes After the alloy melt is fully stirred evenly by electromagnetic stirring, it is introduced into the graphite mold for casting; (b) The ingot is cold-rolled, and the reduction of each rolling pass is 10-20% until the required rolling is achieved. Thickness (0.1-0.5mm).
[0023] The matrix phase of the material has a melting point of 210 degrees, while the ...
Embodiment 3
[0025] A liquid metal thermal interface material with 120-180 degree heat dissipation and no side leakage. In terms of weight percentage, the composition of the alloy is: Al: 0.8wt.%, Co: 0.3wt.%, Ga: 1.2wt.%, V: 0.3wt.%, Zn: 28.5wt.%, Ge: 1.8wt. %, Sb: 3.2wt.%, the balance is indium.
[0026] The preparation method of the above-mentioned heat dissipation material includes the following processing steps: (a) After the alloy is configured according to the required components, it is put into an induction furnace for melting, and is protected by a graphite crucible and argon; heat preservation at 300-400 degrees for 10 minutes After the alloy melt is fully stirred evenly by electromagnetic stirring, it is introduced into the graphite mold for casting; (b) The ingot is cold-rolled, and the reduction of each rolling pass is 10-20% until the required rolling is achieved. Thickness (0.1-0.5mm).
[0027] The melting point of the matrix phase of the material is 210 degrees, while the...
PUM
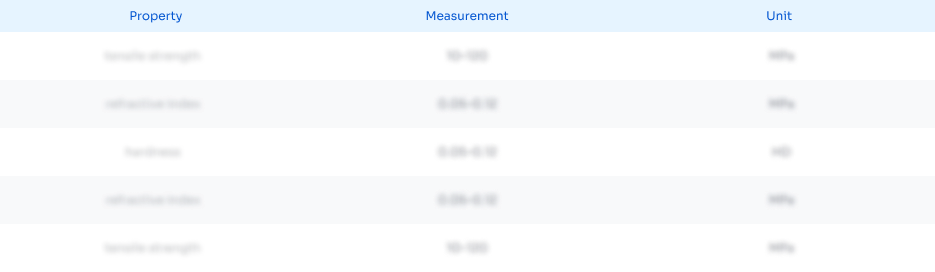
Abstract
Description
Claims
Application Information

- R&D
- Intellectual Property
- Life Sciences
- Materials
- Tech Scout
- Unparalleled Data Quality
- Higher Quality Content
- 60% Fewer Hallucinations
Browse by: Latest US Patents, China's latest patents, Technical Efficacy Thesaurus, Application Domain, Technology Topic, Popular Technical Reports.
© 2025 PatSnap. All rights reserved.Legal|Privacy policy|Modern Slavery Act Transparency Statement|Sitemap|About US| Contact US: help@patsnap.com