Production technology for electronic grade ammonium cerium nitrate
A technology of cerium ammonium nitrate and production process, which is applied in the field of production technology of electronic grade cerium ammonium nitrate, can solve the problems of low yield, high content of non-rare earth metal impurity ions, low purity of cerium ammonium nitrate and the like, so as to improve production efficiency. Effect
- Summary
- Abstract
- Description
- Claims
- Application Information
AI Technical Summary
Problems solved by technology
Method used
Image
Examples
Embodiment 1
[0039] The production technology of electronic grade cerium ammonium nitrate comprises the following steps:
[0040] (1) Add pure water to raw material cerium carbonate, add nitric acid to dissolve and form solution 1, adjust solution 1 to acidity to obtain solution 2, solution 2 is warmed up to 60 DEG C and add hydrogen peroxide, heat preservation reaction 20 minutes; Calculate by weight parts Add 0.8 part of pure water to 1 part of raw material cerium carbonate to form a slurry, add 0.8 part of nitric acid to the slurry to form a solution 1, and adjust the pH to 0.5 to obtain a solution 2; the concentration by weight of the nitric acid is 60%; The ratio of hydrogen peroxide to solution 2 is H 2 o 2 / TREO:0.2%; Fe contained in raw material cerium carbonate 2+ oxidized to Fe 3+ ;
[0041] (2) Add cerium carbonate to adjust the pH value to 2, then adjust the pH value to 4 with ammonium bicarbonate aqueous solution, heat up to 90°C for 35 minutes to obtain a trivalent cerium...
Embodiment 2
[0054] The production technology of electronic grade cerium ammonium nitrate comprises the following steps:
[0055] (1) Add pure water to the raw material cerium carbonate, add nitric acid to dissolve and form solution 1, adjust solution 1 to acidity to obtain solution 2, heat solution 2 to 65° C. and add hydrogen peroxide, and keep warm for 22 minutes; raw material cerium carbonate contains Fe 2+ oxidized to Fe 3+ ; In parts by weight, add 0.9 part of pure water into 1 part of raw material cerium carbonate to form a slurry, add 0.82 part of nitric acid to the slurry to form a solution 1, and adjust the pH to 1.0 to obtain a solution 2; the weight of the nitric acid The percentage concentration is 64%; the ratio of hydrogen peroxide to solution 2 is H 2 o 2 / TREO:0.2%;
[0056] (2) Add cerium carbonate to adjust the pH value to 2.2, then adjust the pH value to 4.2 with ammonium bicarbonate aqueous solution, heat up to 93°C for 30 minutes and obtain a trivalent cerium solu...
Embodiment 3
[0069] The production technology of electronic grade cerium ammonium nitrate comprises the following steps:
[0070](1) Add pure water to raw material cerium carbonate, add nitric acid to dissolve and form solution 1, adjust solution 1 to acidity to obtain solution 2, solution 2 is warmed up to 70 DEG C and add hydrogen peroxide, keep warm for 25 minutes; 1.0 part of pure water is added to 1 part of raw material cerium carbonate to form a slurry, 0.85 part of nitric acid is added to the slurry to form a solution 1, and the pH is adjusted to 1.0 to obtain a solution 2; the concentration by weight of the nitric acid is 68%; The ratio of hydrogen peroxide to solution 2 is H 2 o 2 / TREO:0.2%; Fe contained in raw material cerium carbonate 2+ oxidized to Fe 3+ ;
[0071] (2) Add cerium carbonate to adjust the pH value to 2.5, then adjust the pH value to 4.5 with ammonium bicarbonate aqueous solution, heat up to 95°C for 25 minutes and obtain a trivalent cerium solution; Fe 3+ H...
PUM
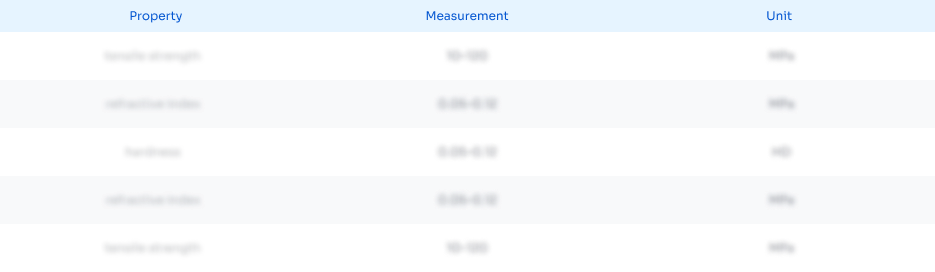
Abstract
Description
Claims
Application Information

- R&D Engineer
- R&D Manager
- IP Professional
- Industry Leading Data Capabilities
- Powerful AI technology
- Patent DNA Extraction
Browse by: Latest US Patents, China's latest patents, Technical Efficacy Thesaurus, Application Domain, Technology Topic, Popular Technical Reports.
© 2024 PatSnap. All rights reserved.Legal|Privacy policy|Modern Slavery Act Transparency Statement|Sitemap|About US| Contact US: help@patsnap.com