Drill rod welding robot production line
A welding robot and production line technology, applied in welding equipment, auxiliary welding equipment, welding/cutting auxiliary equipment, etc., can solve problems such as smoke, low degree of automation, and inability to quickly change models, so as to reduce self-weight deformation and downward deformation , Improve the degree of automation, improve the effect of production efficiency
- Summary
- Abstract
- Description
- Claims
- Application Information
AI Technical Summary
Problems solved by technology
Method used
Image
Examples
Embodiment 1
[0038] combined with Figure 1-3Shown, a kind of drill pipe welding robot production line, comprises power source and water tank 12, also comprises positioner moving track 5 and the positioner installed on positioner moving track 5, one of described positioner moving track 5 A robot moving track 4 is arranged in parallel on the side, and an inverted "L"-shaped cantilever 1 is slidably installed on the robot moving track 4. The cantilever 1 includes columns and beams at right angles to each other, and a robot is hung upside down on the beam. , the other side of the moving track 5 of the positioner is provided with two or more mobile trolleys 6, the positioner includes a positioner headstock 13 and a positioner tailstock 14, the positioner head Seat 13, positioner tailstock 14 are all provided with electric chuck, and described positioner headstock 13, positioner tailstock 14 are respectively connected drive unit, and described drive unit is used for driving positioner headstock...
Embodiment 2
[0042] On the basis of embodiment 1, it also includes a hood-type soot purification device 2, which includes a soot purifier, a soot purification pipeline, a soot net cover and a flexible plastic curtain, and the soot purification pipeline is fixed on the On the above-mentioned cantilever 1, one end of the soot purification pipe is connected to the air outlet of the soot purifier, and the other end of the soot purification pipe is connected through the soot net cover, and a fixing groove is opened around the soot net cover, and the fixation groove A plastic curtain is fixed inside, and the top of the smoke and dust net cover is provided with a through hole for the robot to seal and penetrate.
[0043] When the robot is welding, it is completely in the space surrounded by the fume hood and the plastic curtain. The fume generated by welding can be discharged through the fume purification pipe connected with the fume hood, and purified by the fume purifier to avoid polluting the e...
Embodiment 3
[0046] On the basis of Example 1, in conjunction with the attached Figure 4 and Figure 5 As shown, the auxiliary supporting device 8 includes a lifting mechanism and a traversing mechanism, and the lifting mechanism includes a fixed base 84 on which a lifting motor 81 and a lifting screw 82 are installed. The motor 81 is drivingly connected with the lifting screw 82, the lifting block 83 for supporting the workpiece is installed on the top of the lifting screw 82, and the traversing mechanism includes a traversing motor 87 and is used for installing the fixed seat 84 and The base 85 of the traverse motor 87 is provided with a gear 86 at the bottom end of the base 85, and the gear 86 is driven by the traverse motor 87. The base 85 is provided with guide columns 88 on both sides of the lifting screw 82.
[0047] Further, the lifting block 83 is a cuboid or a cuboid with a V-shaped groove or an inverted trapezoidal groove at its upper end.
[0048] Multiple auxiliary support ...
PUM
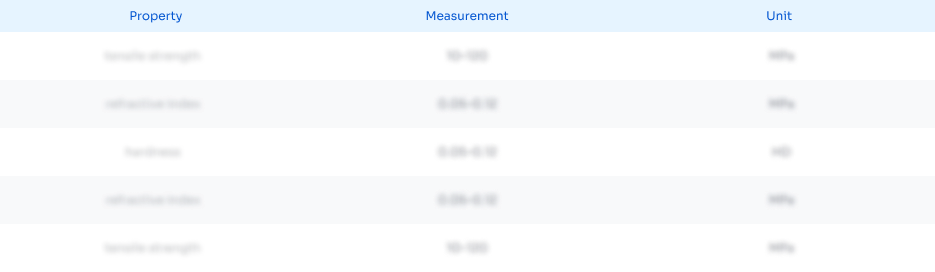
Abstract
Description
Claims
Application Information

- R&D Engineer
- R&D Manager
- IP Professional
- Industry Leading Data Capabilities
- Powerful AI technology
- Patent DNA Extraction
Browse by: Latest US Patents, China's latest patents, Technical Efficacy Thesaurus, Application Domain, Technology Topic, Popular Technical Reports.
© 2024 PatSnap. All rights reserved.Legal|Privacy policy|Modern Slavery Act Transparency Statement|Sitemap|About US| Contact US: help@patsnap.com