Waste white clay recovery and utilization method
A treatment method and technology of waste white clay, which is applied in the field of waste white clay recycling and treatment, can solve the problems of white clay structure damage, energy consumption, etc., and achieve the effect of easing process conditions, reducing safety hazards, and good replacement effect
- Summary
- Abstract
- Description
- Claims
- Application Information
AI Technical Summary
Problems solved by technology
Method used
Examples
Embodiment 1
[0025] (1) Mix 100g of waste clay with 300g of water at 70°C, and after mixing evenly, the obtained material is divided into three layers: solid phase, water phase and oil phase;
[0026] (2) The solid phase obtained after separation in step (1) was mixed with 33mL of treating agent (the treating agent was 20wt% hydrogen peroxide and n-pentadecane, the ratio of hydrogen peroxide and n-pentadecane was 1:1) in Mixing treatment at 80°C, then standing and layering;
[0027] (3) After removing the colloidal asphaltenes in the uppermost layer from the material obtained in step (2), further filter and separate to obtain the filtrate and waste clay, wash the waste clay with water, and then dry it at 80°C to obtain regenerated clay. The oil content of clay is 3.25%, and the activity degree measured by sodium hydroxide titration is 183.
Embodiment 2
[0029] (1) Mix 100g of waste clay with 600g of water at 60°C, and after mixing evenly, the obtained material is divided into three layers: solid phase, water phase and oil phase;
[0030] (2) Mix the solid phase obtained in step (1) with water at 70°C, and the material obtained after mixing evenly is divided into three layers: solid phase, water phase and oil phase;
[0031] (3) Mix the solid phase obtained after step (2) with 40mL of treating agent (the treating agent is 40wt% hydrogen peroxide, the ratio of hydrogen peroxide to n-heptane is 1:6) at 70°C ;
[0032] (4) After removing the colloidal asphaltenes in the uppermost layer from the material obtained in step (3), further filter and separate to obtain the filtrate and waste clay, wash the waste clay with water, and dry at 90°C to obtain regenerated clay, which contains oil The rate was 2.42%, and the activity measured by sodium hydroxide titration was 170.
Embodiment 3
[0034] (1) Mix 100g of waste clay with 450g of water at 100°C, and after mixing evenly, the obtained material is divided into three layers: solid phase, water phase and oil phase;
[0035] (2) Combine the solid phase obtained after the separation in step (1) with 45mL of treating agent (the treating agent is 35wt% hydrogen peroxide and n-decane, the ratio of hydrogen peroxide and n-decane is 1:5) at 75°C Down mixing process, then static layering;
[0036] (3) Remove the colloidal asphaltenes in the uppermost layer from the material obtained in step (2), and further filter and separate to obtain the filtrate and waste clay. The waste clay is washed with water and dried at 95°C to obtain regenerated clay. The regenerated clay is The oil content is 4.78%, and the activity measured by sodium hydroxide titration is 179%.
PUM
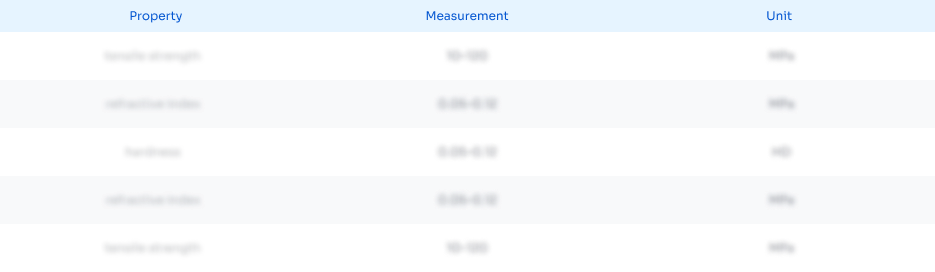
Abstract
Description
Claims
Application Information

- R&D
- Intellectual Property
- Life Sciences
- Materials
- Tech Scout
- Unparalleled Data Quality
- Higher Quality Content
- 60% Fewer Hallucinations
Browse by: Latest US Patents, China's latest patents, Technical Efficacy Thesaurus, Application Domain, Technology Topic, Popular Technical Reports.
© 2025 PatSnap. All rights reserved.Legal|Privacy policy|Modern Slavery Act Transparency Statement|Sitemap|About US| Contact US: help@patsnap.com