Balance beam intelligent welding method based on robot welding production line
A technology of robotic welding and welding methods, applied in welding equipment, comprehensive factory control, comprehensive factory control, etc., can solve the problems of poor weld seam formation in manual welding, increase labor intensity of workers, and heavy grinding workload, etc., and achieve welding parameters Stable and reliable, reduced grinding workload, high welding efficiency
- Summary
- Abstract
- Description
- Claims
- Application Information
AI Technical Summary
Problems solved by technology
Method used
Image
Examples
Embodiment Construction
[0025] The technical solutions of the present invention will be further described below in conjunction with the accompanying drawings and embodiments.
[0026] Please combine figure 1 As shown, the intelligent welding method of a balance beam based on the robot welding production line provided by the present invention is divided into super large balance beam welding station 1, large balance beam welding station 2, and medium balance beam welding station according to the shape and size of the balance beam. Position 3, small balance beam welding position 4, special-shaped balance beam welding position 5, extra large balance beam buffer position 6, large balance beam buffer position 7, medium and small balance beam buffer position 18, small and medium balance beam buffer Station 2 9, extra large and large balance beam loading and unloading station 10, medium and small balance beam loading and unloading station 11, extra large and large balance beam flipping station 12, extra larg...
PUM
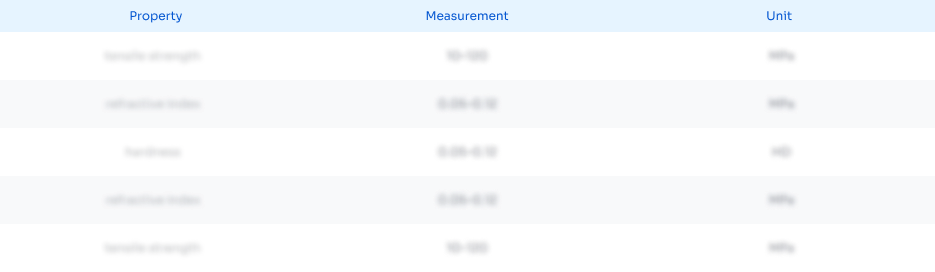
Abstract
Description
Claims
Application Information

- R&D Engineer
- R&D Manager
- IP Professional
- Industry Leading Data Capabilities
- Powerful AI technology
- Patent DNA Extraction
Browse by: Latest US Patents, China's latest patents, Technical Efficacy Thesaurus, Application Domain, Technology Topic, Popular Technical Reports.
© 2024 PatSnap. All rights reserved.Legal|Privacy policy|Modern Slavery Act Transparency Statement|Sitemap|About US| Contact US: help@patsnap.com