Low temperature resistant high speed permanent magnet motor high strength rotor structure
A permanent magnet motor, rotor structure technology, applied in the magnetic circuit shape/style/structure, magnetic circuit rotating parts and other directions, can solve the problems of poor rotor heat dissipation, easy breakage, poor mechanical strength and so on
- Summary
- Abstract
- Description
- Claims
- Application Information
AI Technical Summary
Problems solved by technology
Method used
Image
Examples
Embodiment Construction
[0018] In order to make the technical means, creative features, goals and effects achieved by the present invention easy to understand, the invention will be further elaborated below in conjunction with specific embodiments.
[0019] see Figure 1 to Figure 4 , High-strength rotor structure of low-temperature resistant high-speed permanent magnet motor, including rotor core 5, permanent magnet pole 3, rib 2, rotating shaft 6, and cooling holes 10.
[0020] The outer side of the rotor core 5 is fixed with permanent magnet poles 3 equidistantly arranged along the circumferential direction, the rotor core 5 is connected with the permanent magnet poles 3 through an anaerobic adhesive layer 9, and the outer side of the permanent magnet poles 3 is pasted with a copper plating layer 4 .
[0021] A first cooling branch 7 is provided between the permanent magnet poles 3, and each of the permanent magnet poles 3 is unevenly divided into No. 1 permanent magnet 3.1, No. 2 permanent magne...
PUM
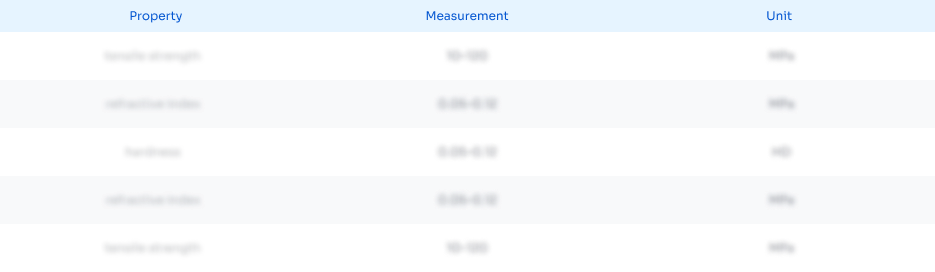
Abstract
Description
Claims
Application Information

- R&D
- Intellectual Property
- Life Sciences
- Materials
- Tech Scout
- Unparalleled Data Quality
- Higher Quality Content
- 60% Fewer Hallucinations
Browse by: Latest US Patents, China's latest patents, Technical Efficacy Thesaurus, Application Domain, Technology Topic, Popular Technical Reports.
© 2025 PatSnap. All rights reserved.Legal|Privacy policy|Modern Slavery Act Transparency Statement|Sitemap|About US| Contact US: help@patsnap.com