Method for continuously producing cyclododecatriene
A technology for cyclododecatriene and butadiene, applied in the field of continuous production of cyclododecatriene, can solve the problems of low catalytic efficiency, long residence time, unreasonable quenching process, etc., and achieve good solubility Effect
- Summary
- Abstract
- Description
- Claims
- Application Information
AI Technical Summary
Problems solved by technology
Method used
Image
Examples
Embodiment 1
[0070] Step 1, Catalyst Preparation: Catalyst Preparation Reactor A is a three-pot reactor in series, and the catalyst raw material is fed from the first pot. The composition is shown in Table 1.
[0071] Table 1. Catalyst feed amount
[0072]
[0073] Control the liquid level to ensure the residence time The jacket controls the temperature at 30°C and the residence time is 10min.
[0074] Step 2, butadiene impurity removal: add butadiene: 300kg / h and trimethylaluminum: 30g / h to impurity removal stirred tank B, mixing temperature 15°C, control residence time 2min, discharge into polymerization reaction kettle C.
[0075] Step 3, reaction: The catalyst solution obtained in step 1 and the butadiene stream after removal of impurities obtained in step 2 enter the polymerization reactor C at a total rate of 485.6 kg / h, the reaction temperature is 100° C., and the residence time is 100 min.
[0076] Step 4, aging: the reaction solution 4 is discharged from the reactor into the ...
Embodiment 2
[0092] Step 1, Catalyst preparation: Catalyst preparation reactor A is a three-pot reactor in series, and the catalyst raw material is fed from the first pot. The composition is shown in Table 4.
[0093] Table 4. Catalyst feed amount
[0094]
[0095] Control the liquid level to ensure the residence time The jacket controls the temperature at 60°C and the residence time is 5min.
[0096] Step 2, butadiene impurity removal: add butadiene 202kg / h and trimethylaluminum 4g / h to the impurity removal stirring reactor B, mix at 0°C, control the residence time for 5min, and discharge the material into the polymerization reactor c.
[0097] Step 3, reaction: the catalyst solution obtained in step 1 and the butadiene stream 12 after removal of impurities obtained in step 2 enter a three-pot series polymerization reactor at a total rate of 388 kg / h, with a reaction temperature of 90° C. and a residence time of 200 min.
[0098] Step 4, aging: the reaction liquid 4 is discharged fro...
Embodiment 3
[0105] Step 1, Catalyst preparation: Catalyst preparation reactor A is a three-pot reactor in series, and the catalyst raw material is fed from the first pot. The composition is shown in Table 6.
[0106] Table 6. Catalyst feed amount of embodiment 3
[0107]
[0108] Control the liquid level to ensure the residence time The jacket controls the temperature at 20°C and the residence time is 60min.
[0109] Step 2, butadiene impurity removal: add butadiene 252kg / h and triisobutylaluminum 10g / h to the impurity removal stirring impurity removal kettle B, the mixing temperature is 10°C, the residence time is controlled for 1min, and the material is discharged into the polymerization Reactor C.
[0110] Step 3, reaction: a total of 439 kg / h of the catalyst solution obtained in step 1 and the butadiene obtained in step 2 entered the three-pot series polymerization reactor C with a reaction temperature of 150° C. and a residence time of 30 min.
[0111] Step 4, Aging: The reactio...
PUM
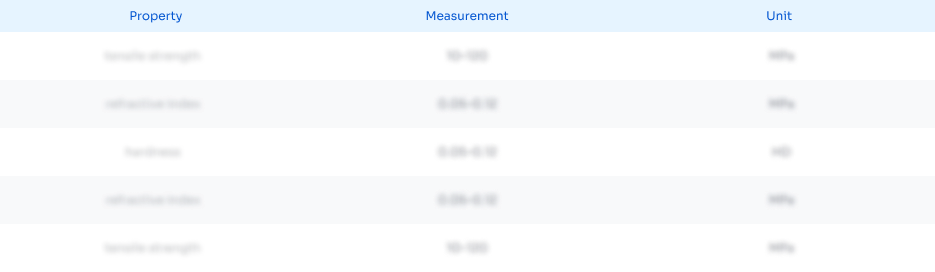
Abstract
Description
Claims
Application Information

- R&D
- Intellectual Property
- Life Sciences
- Materials
- Tech Scout
- Unparalleled Data Quality
- Higher Quality Content
- 60% Fewer Hallucinations
Browse by: Latest US Patents, China's latest patents, Technical Efficacy Thesaurus, Application Domain, Technology Topic, Popular Technical Reports.
© 2025 PatSnap. All rights reserved.Legal|Privacy policy|Modern Slavery Act Transparency Statement|Sitemap|About US| Contact US: help@patsnap.com