PPS/PA66/graphene composite material and preparation method thereof
A composite material and graphene technology, applied in the field of polymer materials, can solve problems such as low melt strength, melt viscosity affecting the stability of injection molding extrusion molding process, and unstable melt viscosity
- Summary
- Abstract
- Description
- Claims
- Application Information
AI Technical Summary
Problems solved by technology
Method used
Image
Examples
Embodiment 1-10
[0047] Shown in Table 1 is the mass ratio of each component used in Examples 1-10.
[0048] The preparation method steps of described PPS / PA66 / graphene are as follows:
[0049] (1) Mix graphene and distilled water, put them into XR-LU08 ultrasonic cleaning machine of Changzhou Xinren Ultrasonic Equipment Co., Ltd. and ultrasonically mix for 1.5-2h,
[0050] (2) in the graphene mixed solution after the ultrasonic mixing of gained in (1), further add coupling agent and emulsifier according to the mass ratio shown in table 1, and ultrasonic mixing 5-15min;
[0051] (3) According to the mass ratio shown in Table 1, PA powder is blended with graphene aqueous solution, and the mixed solution is put into a grinding dish and ground for 2-3 hours. °C, and then put the resultant into a vacuum drying oven to dry at 80±5 °C to obtain a graphene pre-dispersion;
[0052] (4) Weigh EMG particles, PPS, PA66, and antioxidant 1010 according to the mass ratio shown in Table 1; dry the PPS in a...
Embodiment 11-15
[0070] In Examples 11-15, graphene is dispersed by blending and masticating EMG and graphene to enhance the dispersion of graphene, and utilize the synergistic effect of EMG and graphene to adjust the melt index of the composite material , to enhance the processing performance of composite materials. Its specific operation is as follows:
[0071] According to the formula shown in Table 4,
[0072] (1) Mix the weighed EMG on the XK-160 mill roller of Changzhou First Rubber and Plastic Equipment Co., Ltd.,
[0073] (2) add Graphene to the EMG of refining, continue refining and disperse on roller, obtain EMG / Graphene blend;
[0074] (3) Standby after pulverizing the EMG / graphene blend;
[0075] (4) Dry the polyphenylene sulfide in a vacuum oven at 90°C for 2-4 hours in advance; dry the polyamide in a vacuum oven at 90°C for 10 hours in advance, then weigh the polyphenylene sulfide and polyamide, Mix with graphene pre-dispersion and antioxidant, add Coperion (Nanjing) Machiner...
PUM
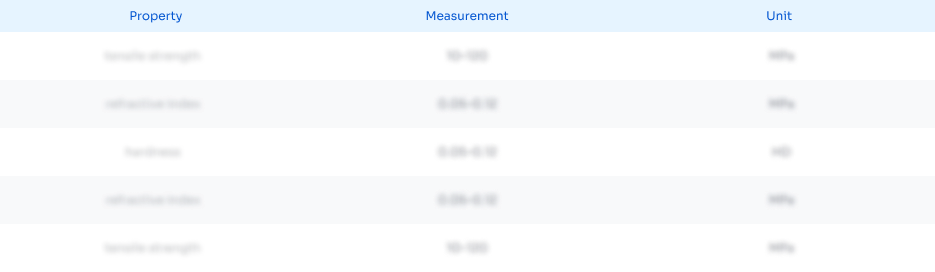
Abstract
Description
Claims
Application Information

- Generate Ideas
- Intellectual Property
- Life Sciences
- Materials
- Tech Scout
- Unparalleled Data Quality
- Higher Quality Content
- 60% Fewer Hallucinations
Browse by: Latest US Patents, China's latest patents, Technical Efficacy Thesaurus, Application Domain, Technology Topic, Popular Technical Reports.
© 2025 PatSnap. All rights reserved.Legal|Privacy policy|Modern Slavery Act Transparency Statement|Sitemap|About US| Contact US: help@patsnap.com