High-crack-resistance wear-resistant terrace material and preparation method thereof
A floor material with high crack resistance technology, applied in the field of building materials, can solve the problems of surface cracks, easy cracking, high crack occurrence rate, etc., and achieve the effect of hard surface, strong compression resistance and long service life
- Summary
- Abstract
- Description
- Claims
- Application Information
AI Technical Summary
Problems solved by technology
Method used
Image
Examples
preparation example Construction
[0081] A preparation method of a highly crack-resistant and wear-resistant floor material, comprising the following preparation steps:
[0082] Step 1: Add Portland cement, aggregate, admixture, water reducer, redispersible latex powder, and early strength agent into the reactor and stir for 10 to 65 minutes to form a mixed solution;
[0083] Step 2: Add fibers to the mixture in Step 1, and stir for 10-60 minutes to obtain flooring materials.
[0084] In this embodiment, the reactor is a dry powder mortar mixer.
[0085] After the fiber is mixed, it can act as a high elastic modulus material compared with the plastic slurry, and the surface adsorption viscosity and mechanical tooth force of the cement slurry and the fiber material will significantly improve the cracking resistance of the concrete material, and at the same time enhance its plastic tensile strength. Strength, and because the dehydration shrinkage stress is significantly smaller than the plastic tensile strength o...
Embodiment 1
[0087] Embodiment one: by preparing 1000 kilograms of emery sand wear-resistant floors, add 377.5 kilograms of Portland cement that the strength grade is PⅡ42.5R by the following weight, 18 kilograms of silica fume, and 600 kilograms of quartz sand with a mesh number of 20, 0.2 kg of polycarboxylic acid high-efficiency water reducer, 2 kg of ethylene and vinyl acetate copolymer latex powder, 2 kg of calcium formate and stir in the dry powder mortar mixer for 30 minutes, then add 0.3 kg of polypropylene fiber after the stirring is completed, and stir for 40 minutes to obtain Product of the present invention.
Embodiment 2
[0088] Embodiment two: by preparing 1000 kilograms of emery sand wear-resistant floor meter, adding strength grade is 375 kilograms of portland cement of PⅡ42.5R by the following weight, 20 kilograms of silica fumes, 600 kilograms of quartz sands of 30 meshes, 0.2 kg of naphthalenesulfonic acid formaldehyde condensate, 2 kg of latex powder of vinyl acetate and vinyl tertiary carbonate copolymer, 2 kg of calcium formate and stir in the dry powder mortar mixer for 30 minutes, add 0.8 kg of polypropylene fiber after the stirring is completed, and stir for 40 Minutes, obtain product of the present invention.
PUM
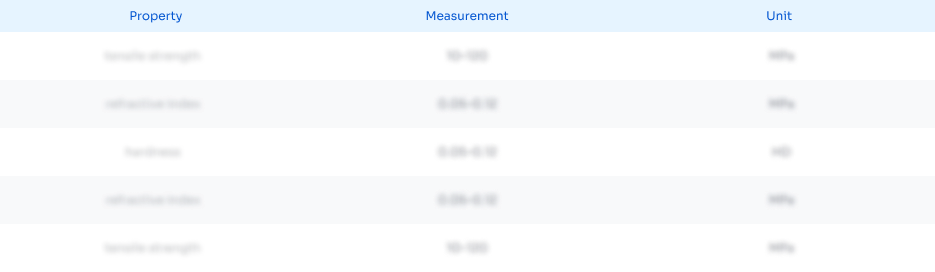
Abstract
Description
Claims
Application Information

- R&D Engineer
- R&D Manager
- IP Professional
- Industry Leading Data Capabilities
- Powerful AI technology
- Patent DNA Extraction
Browse by: Latest US Patents, China's latest patents, Technical Efficacy Thesaurus, Application Domain, Technology Topic, Popular Technical Reports.
© 2024 PatSnap. All rights reserved.Legal|Privacy policy|Modern Slavery Act Transparency Statement|Sitemap|About US| Contact US: help@patsnap.com