Method for deeply extracting vanadium by utilizing alkaline tailings
A tailings and alkaline technology, which is applied in the field of deep vanadium extraction using alkaline tailings, can solve the problems of complex process, high energy consumption, and recovery outweighing the loss, and achieve the effects of simple process, short process and cost saving.
- Summary
- Abstract
- Description
- Claims
- Application Information
AI Technical Summary
Problems solved by technology
Method used
Examples
Embodiment 1
[0033] (1) Ingredients: Mix the alkaline tailings (Na is 10%, V is 0.8%, and moisture is 25%) with vanadium-containing materials (V is 1.5%) at a mass ratio of 0.1:1 to obtain a mixture ;
[0034] (2) Roasting: Place the mixed material in a muffle furnace and roast at 820°C for 1.5 hours to obtain roasted clinker;
[0035] (3) Leaching: leaching the roasted clinker with 85°C hot water, and filtering to obtain a vanadium-containing leaching solution;
[0036] (4) Washing: Wash the leaching residue with hot water at 80°C to obtain the vanadium extraction tailings, and the obtained washing water is returned to the vanadium-containing leaching solution.
[0037] After testing, the obtained vanadium extraction tailings contained vanadium at 0.55 wt%, and the leaching rate of vanadium was 88.7%.
Embodiment 2
[0039] (1) Ingredients: Mix the alkaline tailings (12% for Na, 0.9% for V, and 22% for water) with vanadium-containing materials (V for 1.8%) at a mass ratio of 0.2:1 to obtain a mixture ;
[0040] (2) Roasting: Place the mixture in a muffle furnace and roast at 800°C for 1 hour to obtain roasted clinker;
[0041] (3) Leaching: leaching the roasted clinker with hot water at 90°C, and filtering to obtain a vanadium-containing leaching solution;
[0042] (4) Washing: Wash the leaching residue with hot water at 85°C to obtain the vanadium extraction tailings, and the obtained washing water is returned to the vanadium-containing leaching solution.
[0043] After testing, the vanadium extraction tailings contained 0.52wt% vanadium, and the vanadium leaching rate was 90%.
Embodiment 3
[0045] (1) Ingredients: Mix the alkaline tailings (Na is 8%, V is 0.75%, and the water content is 20%) and vanadium-containing materials (V is 1.2%) at a mass ratio of 0.15:1 to obtain a mixture ;
[0046] (2) Roasting: Place the mixture in a muffle furnace and roast for 0.5h at 750°C to obtain roasted clinker;
[0047] (3) Leaching: leaching the roasted clinker with 95°C hot water, and filtering to obtain a vanadium-containing leaching solution;
[0048] (4) Washing: Wash the leaching residue with hot water at 80°C to obtain the vanadium extraction tailings, and the obtained washing water is returned to the vanadium-containing leaching solution.
[0049] After testing, the vanadium extraction tailings contained 0.58 wt% vanadium, and the leaching rate of vanadium was 86.1%.
PUM
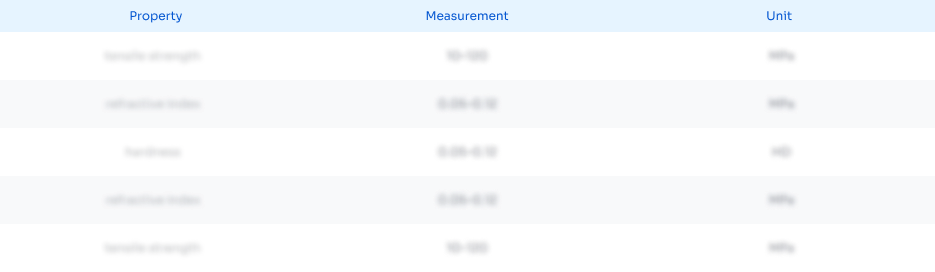
Abstract
Description
Claims
Application Information

- R&D Engineer
- R&D Manager
- IP Professional
- Industry Leading Data Capabilities
- Powerful AI technology
- Patent DNA Extraction
Browse by: Latest US Patents, China's latest patents, Technical Efficacy Thesaurus, Application Domain, Technology Topic, Popular Technical Reports.
© 2024 PatSnap. All rights reserved.Legal|Privacy policy|Modern Slavery Act Transparency Statement|Sitemap|About US| Contact US: help@patsnap.com