Application of graphene oxide conductive slurry in hole blackening direct electroplating
A technology of conductive paste and graphene, applied in electrolytic inorganic material plating, electrical components, printed circuits, etc., can solve the problems of strict requirements on the density of conductive layers and many steps, so as to improve the efficiency of electroplating, combine firmly, and prevent aggregation The effect of the phenomenon
- Summary
- Abstract
- Description
- Claims
- Application Information
AI Technical Summary
Problems solved by technology
Method used
Image
Examples
Embodiment 1
[0032] A kind of application of graphene oxide electroconductive paste in black hole direct electroplating, comprising preparing graphene oxide electroconductive paste and using the obtained graphene oxide electroconductive paste to carry out black hole direct electroplating, the steps are:
[0033] A. Preparation of graphene oxide conductive paste
[0034] A1) Preparation of graphite oxide powder: immerse 10g of natural flake graphite in the mixed acid of 100ml of concentrated sulfuric acid and 20ml of concentrated nitric acid, filter after soaking at room temperature for 12h, wash the filter cake with deionized water until the pH value of the lotion is between 6-7 After a period of time, the filter cake was placed in a vacuum drying oven and dried at 70°C for 4 hours to obtain graphite oxide powder;
[0035] A2) Modified graphite oxide: Soak graphite oxide powder in hydrazine hydrate at room temperature for 10 hours, filter after soaking, wash the filter cake with deionized ...
Embodiment 2
[0044] A kind of application of graphene oxide electroconductive paste in black hole direct electroplating, comprising preparing graphene oxide electroconductive paste and using the obtained graphene oxide electroconductive paste to carry out black hole direct electroplating, the steps are:
[0045] A. Preparation of graphene oxide conductive paste
[0046] A1) Preparation of graphite oxide powder: immerse 10g of natural flake graphite in the mixed acid of 100ml of concentrated sulfuric acid and 20ml of concentrated nitric acid, filter after soaking at room temperature for 16h, wash the filter cake with deionized water until the pH value of the lotion is between 6-7 After a period of time, the filter cake was placed in a vacuum drying oven and dried at 65°C for 5 hours to obtain graphite oxide powder;
[0047] A2) Modified graphite oxide: Soak graphite oxide powder in hydrazine hydrate for 9 hours at room temperature, filter after soaking, wash the filter cake with deionized w...
Embodiment 3
[0056] A kind of application of graphene oxide electroconductive paste in black hole direct electroplating, comprising preparing graphene oxide electroconductive paste and using the obtained graphene oxide electroconductive paste to carry out black hole direct electroplating, the steps are:
[0057] A. Preparation of graphene oxide conductive paste
[0058] A1) Preparation of graphite oxide powder: immerse 10g of natural flake graphite in the mixed acid of 100ml of concentrated sulfuric acid and 20ml of concentrated nitric acid, filter after soaking at room temperature for 18h, wash the filter cake with deionized water until the pH value of the lotion is between 6-7 After a period of time, the filter cake was placed in a vacuum drying oven and dried at 60°C for 6 hours to obtain graphite oxide powder;
[0059] A2) Modified graphite oxide: Soak graphite oxide powder in hydrazine hydrate at room temperature for 8 hours, filter after soaking, wash the filter cake with deionized w...
PUM
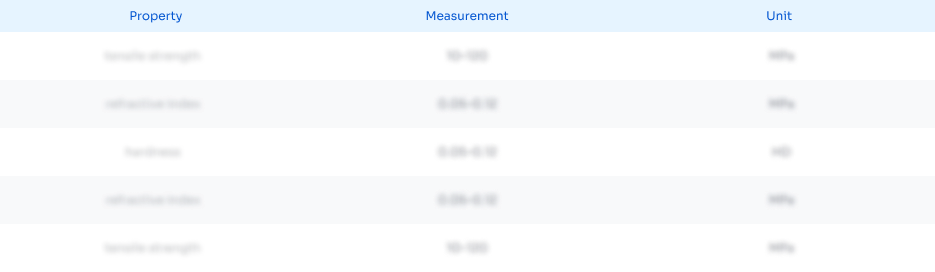
Abstract
Description
Claims
Application Information

- Generate Ideas
- Intellectual Property
- Life Sciences
- Materials
- Tech Scout
- Unparalleled Data Quality
- Higher Quality Content
- 60% Fewer Hallucinations
Browse by: Latest US Patents, China's latest patents, Technical Efficacy Thesaurus, Application Domain, Technology Topic, Popular Technical Reports.
© 2025 PatSnap. All rights reserved.Legal|Privacy policy|Modern Slavery Act Transparency Statement|Sitemap|About US| Contact US: help@patsnap.com