Non-contact laser ultrasonic nondestructive testing system and method applicable to any curved surface
A laser ultrasonic and non-destructive testing technology, which is applied in the direction of material analysis using sound waves/ultrasonic waves/infrasonic waves, measuring devices, and material analysis through optical means. Time and other issues, to achieve the effect of improving detection accuracy and detection efficiency
- Summary
- Abstract
- Description
- Claims
- Application Information
AI Technical Summary
Problems solved by technology
Method used
Image
Examples
Embodiment 1
[0042] Such as figure 1 and figure 2 As shown, this embodiment discloses a non-contact laser ultrasonic nondestructive testing system for arbitrary curved surfaces, the testing system mainly includes an ultrasonic excitation unit 2, an ultrasonic detection unit 9, a mechanical scanning unit 13, and a signal acquisition and processing unit 16. The ultrasonic excitation unit 2 is set as a pulsed laser 1 . The ultrasonic detection unit 9 includes a first mirror 3 , a second mirror 4 , an optical medium 5 , a continuous laser 6 , a beam splitter 7 , and a photodetector 8 . The mechanical scanning unit 13 includes a manipulator 10 and a controller 11 . The signal acquisition and processing unit 16 includes a signal conditioning device 14 , a data acquisition card 15 , and a computer 12 . In the present invention, the computer 12 of the manipulator 10 realizes the planning of the scanning path of any curved surface by optically exciting and receiving ultrasonic waves on the sam...
Embodiment 2
[0067] combine figure 1 and figure 2 As shown, this embodiment provides a non-contact laser ultrasonic non-destructive testing system and method for arbitrary curved surfaces, the purpose of which is to meet the testing requirements of existing complex structural parts, while improving the testing accuracy and efficiency. The non-contact laser ultrasonic nondestructive testing system for arbitrary curved surfaces consists of excitation unit, detection unit, scanning unit, acquisition and processing unit, including the following components:
[0068] Pulse laser 1, ultrasonic detection unit 9 composed of reflector, reflector, optical medium 5, continuous laser 6, beam splitter 7, photoelectric detector 8, composed of six degrees of freedom manipulator 10, controller 11, computer 12 The mechanical scanning unit 13 is a signal acquisition and processing unit 16 composed of a signal conditioning device 14 , a data acquisition card 15 and a computer 12 .
[0069] Fix the test obj...
PUM
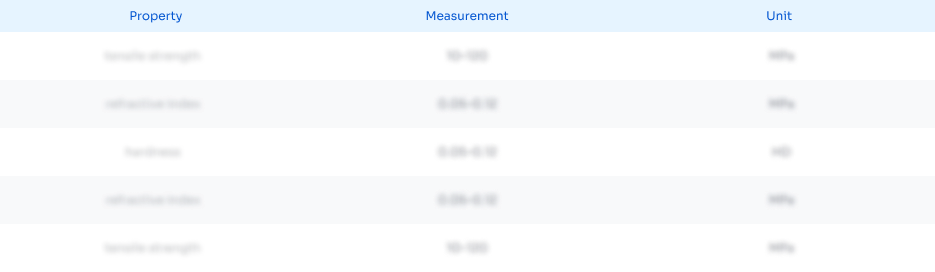
Abstract
Description
Claims
Application Information

- R&D Engineer
- R&D Manager
- IP Professional
- Industry Leading Data Capabilities
- Powerful AI technology
- Patent DNA Extraction
Browse by: Latest US Patents, China's latest patents, Technical Efficacy Thesaurus, Application Domain, Technology Topic, Popular Technical Reports.
© 2024 PatSnap. All rights reserved.Legal|Privacy policy|Modern Slavery Act Transparency Statement|Sitemap|About US| Contact US: help@patsnap.com