Manufacturing technology of thin-wall high-lead bearing brush for main engine of ship
A technology of ship main engine and manufacturing process, applied in the field of ship parts, can solve the problems of impurities in lubricating oil, damage to sliding bearings, abnormal viscosity, etc., and achieve the effects of high precision, flexible adjustment, and good auxiliary function.
- Summary
- Abstract
- Description
- Claims
- Application Information
AI Technical Summary
Problems solved by technology
Method used
Image
Examples
Embodiment Construction
[0014] The present invention is carried out according to the following steps:
[0015] 1) Fine-grinding the bearing bush after enamelling. When machining the bearing bush, the outer circle, inner circle, one end face and chamfer are processed with the axis of the cylinder as the positioning reference, and then the other end face is machined based on the processed end face. , and then machine the groove on the inner surface;
[0016] 2) When machining the outermost slot, the end face is used as the benchmark, and the milling cutter is used for direct milling. After the processing is completed, the second slot is processed at the top edge of the processed slot, and so on until the end of processing.
[0017] Further, when processing the inner circle, the following auxiliary tooling is used, and the structural form of the auxiliary tooling is: sleeved on the outer surface of the bearing bush, and the inner contour of the tooling and the outer surface contour of the bearing bush a...
PUM
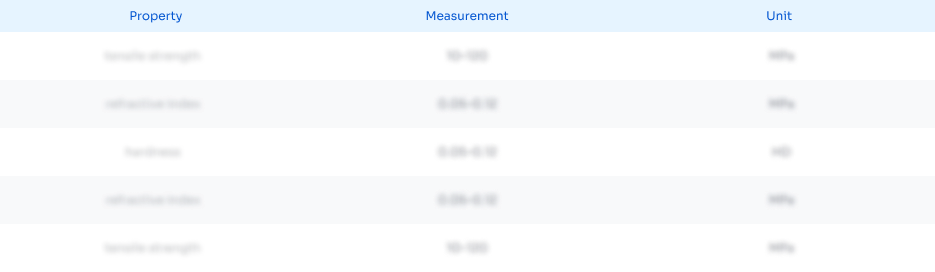
Abstract
Description
Claims
Application Information

- R&D Engineer
- R&D Manager
- IP Professional
- Industry Leading Data Capabilities
- Powerful AI technology
- Patent DNA Extraction
Browse by: Latest US Patents, China's latest patents, Technical Efficacy Thesaurus, Application Domain, Technology Topic, Popular Technical Reports.
© 2024 PatSnap. All rights reserved.Legal|Privacy policy|Modern Slavery Act Transparency Statement|Sitemap|About US| Contact US: help@patsnap.com