Automobile ceramic brake and preparation method thereof
A technology of brake pads and ceramics, applied in the field of ceramic brake pads, can solve problems such as weak toughness, impact damage, uneven mixing of adhesives, etc., to achieve improved wear resistance, high strength heat resistance, and enhanced friction coefficient and toughness effects
- Summary
- Abstract
- Description
- Claims
- Application Information
AI Technical Summary
Problems solved by technology
Method used
Examples
Embodiment 1
[0023] A kind of automobile ceramic brake pad, its raw material comprises by weight: 26 parts of ceramic fiber, 3 parts of high carbon graphite, 14 parts of fluoroapatite, 7 parts of antimony sulfide, 3 parts of chromite, 15 parts of inorganic binder, copper 13 parts fiber and 5 parts barite.
[0024] Step 1: Ingredients: Accurately weigh a certain amount of ceramic fiber, high-carbon graphite, fluoroapatite, antimony sulfide, chromite, copper fiber and barite, and crush them separately, and filter them through different sizes Filter through a sieve, and place the above-mentioned material after filtering in a mixer, and then weigh a quantitative amount of inorganic binder;
[0025] Step 2: Mixing: Start the mixer, place the inorganic binder at the discharge inlet of the mixer, control the speed of the inorganic binder discharge, and make the mixer work while the inorganic binder Put it into the mixer completely in 1 minute, and then stir the mixture for 3 minutes;
[0026] S...
Embodiment 2
[0030] A kind of automobile ceramic brake pad, its raw material comprises by weight: 27 parts of ceramic fiber, 3.5 parts of high-carbon graphite, 15 parts of fluoroapatite, 8 parts of antimony sulfide, 4 parts of chromite, 16 parts of inorganic binder, 15 parts of copper fiber and 6 parts of barite.
[0031] Step 1: Ingredients: Accurately weigh a certain amount of ceramic fiber, high-carbon graphite, fluoroapatite, antimony sulfide, chromite, copper fiber and barite, and crush them separately, and filter them through different sizes Filter through a sieve, and place the above-mentioned material after filtering in a mixer, and then weigh a quantitative amount of inorganic binder;
[0032] Step 2: Mixing: Start the mixer, place the inorganic binder at the discharge inlet of the mixer, control the speed of the inorganic binder discharge, and make the mixer work while the inorganic binder Put it into the mixer completely in 1.5 minutes, and then stir the mixture for 3.5 minutes...
Embodiment 3
[0037] An automotive ceramic brake pad, characterized in that: its raw materials include by weight: 28 parts of ceramic fiber, 4 parts of high-carbon graphite, 20 parts of fluoroapatite, 9 parts of antimony sulfide, 5 parts of chromite, inorganic adhesive 18 parts of agent, 18 parts of copper fiber and 8 parts of barite.
[0038] Step 1: Ingredients: Accurately weigh a certain amount of ceramic fiber, high-carbon graphite, fluoroapatite, antimony sulfide, chromite, copper fiber and barite, and crush them separately, and filter them through different sizes Filter through a sieve, and place the above-mentioned material after filtering in a mixer, and then weigh a quantitative amount of inorganic binder;
[0039] Step 2: Mixing: Start the mixer, place the inorganic binder at the discharge inlet of the mixer, control the speed of the inorganic binder discharge, and make the mixer work while the inorganic binder Put it into the mixer completely in 2 minutes, and stir the mixture f...
PUM
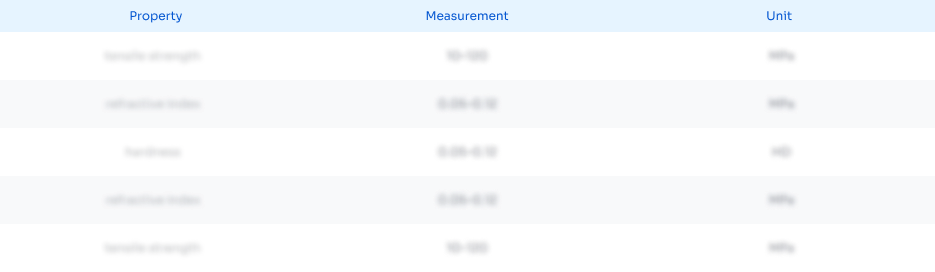
Abstract
Description
Claims
Application Information

- R&D
- Intellectual Property
- Life Sciences
- Materials
- Tech Scout
- Unparalleled Data Quality
- Higher Quality Content
- 60% Fewer Hallucinations
Browse by: Latest US Patents, China's latest patents, Technical Efficacy Thesaurus, Application Domain, Technology Topic, Popular Technical Reports.
© 2025 PatSnap. All rights reserved.Legal|Privacy policy|Modern Slavery Act Transparency Statement|Sitemap|About US| Contact US: help@patsnap.com